A quick introduction to Additive Manufacturing
Understand the fundamentals, key process steps, and the value of AM in today's industrial landscape
Additive Manufacturing (AM), commonly known as industrial 3D printing, is a transformative production method where objects are built layer by layer directly from digital models. Unlike traditional manufacturing—which often removes material from a block—AM adds material only where needed, enabling new design possibilities and greater efficiency for complex or low-volume parts. This section introduces the key principles of AM, explains the core process steps from CAD to finished part, and provides an overview of commonly used terms. You’ll also gain insight into the benefits AM offers, the challenges it faces, and the foundational knowledge needed to make informed decisions about when and how to apply it.
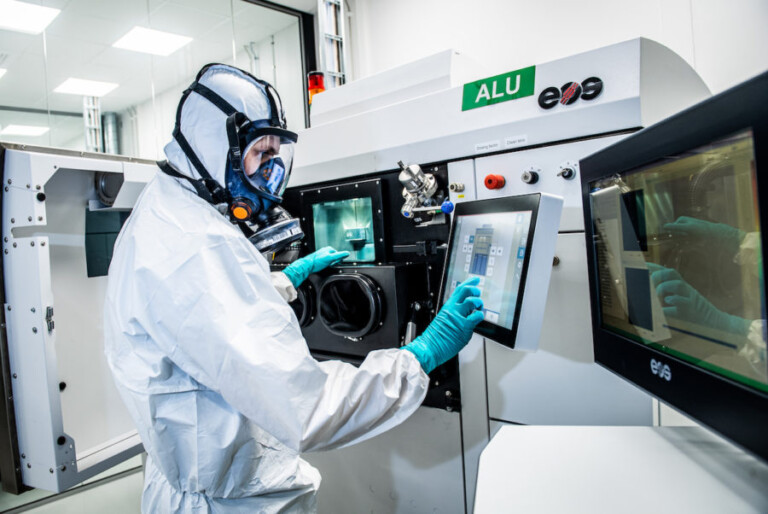
What you will learn in this section
What Is AM and How It Works
Gain a clear understanding of what Additive Manufacturing is, how it differs from traditional methods, and the main process steps from CAD to finished part.
Benefits & Limitations of AM
Explore when and why to use AM, uncovering its key advantages—such as design freedom and small-batch efficiency—as well as its current technological challenges.
Design Considerations & Terminology
Learn essential AM terminology, the role of support structures, and how to approach part design to fully leverage AM's potential.
What you will find in this section
Definition
A definition of Additive Manufacturing
Additive Manufacturing (AM), also known as industrial 3D printing, is the process of creating objects from 3D-model data layer-by-layer, as opposed to subtractive manufacturing methodologies.
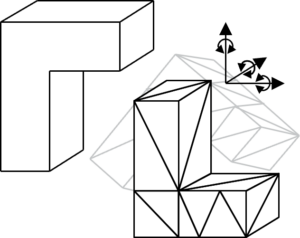
CAD
CAD
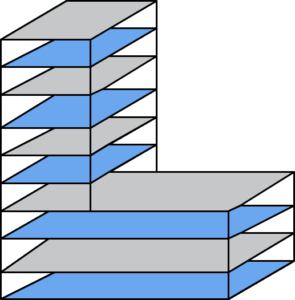
Sliced Data
Sliced Data

Additive Process
Additive Process
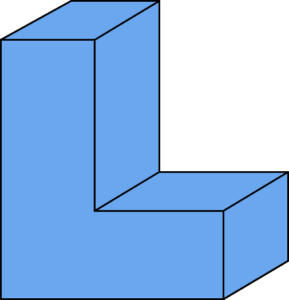
Finished Part
Finished Part
Additive Manufacturing includes a wide range of technologies and terminologies. In order to make a clear distinction between AM and other manufacturing technologies, ASTM first published standard F2792 in 2009 with a clear definition, clustering all AM processes into 7 sub-categories. We will give an overview of these categories later in this course.
Selected terminologies for Additive Manufacturing
Over the years, several terminologies have emerged. While Rapid Prototyping (RP) has been most commonly used in the early days, Additive Manufacturing has become the standard terminology in an industrial context today. Other terms such as industrial 3D printing, are often used interchangeably and can be found on the right. Besides these general terminologies, several companies have coined proprietary terminologies for their processes such as Multi Jet Fusion by HP or the MoldJet Technology by Tritone.
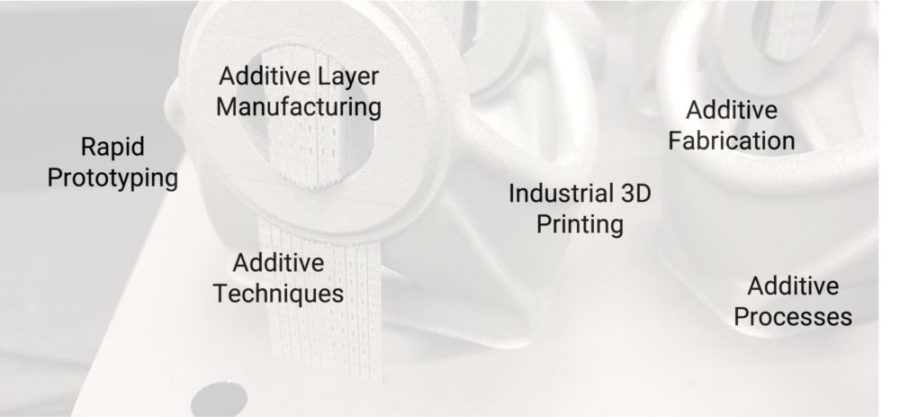
Benefits
AM with benefits for complex parts with low production volume
Additive Manufacturing is often seen as the “holy grail”, some people going as far that it will completely replace conventional manufacturing technologies. We usually describe AM as another tool in the toolbox that brings several benefits, but also a variety of challenges.
As of today, Additive Manufacturing is generally addressing a niche where conventional manufacturing lacks competitiveness. This often covers applications with a low production volume and high complexity. Future developments will continuously increase the productivity and thus reduce the costs. This will lead to a bigger overlap between the technologies and thus more applications where AM is competitive.
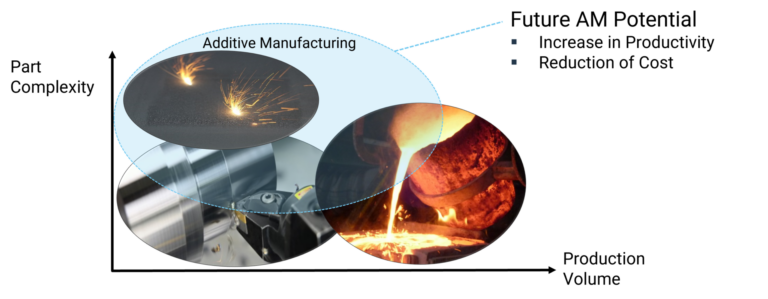
Cost vs. batch size
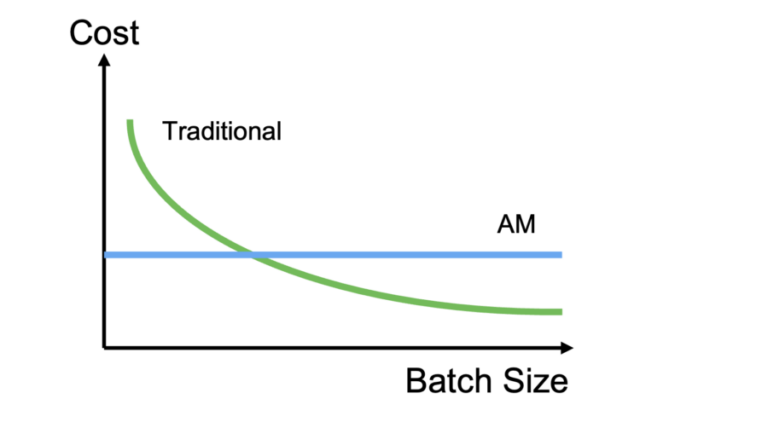
Since Additive Manufacturing is a digital process where no individual tools are required and the CAD model acts as production data, it often has cost benefits compared to traditional technologies for small batch sizes. In a simplified way, there are no economies of scale, meaning that costs do not decrease with the batch size. Therefore, Additive Manufacturing is specifically suitable for low batch sizes.
Cost vs. complexity
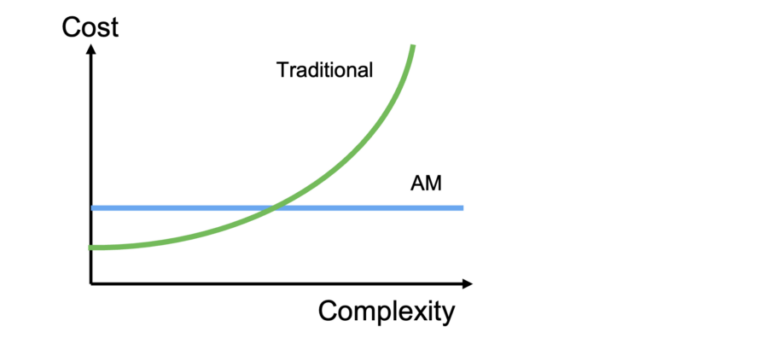
Complexity is no cost driver for Additive Manufacturing opposed to most traditional technologies. The cost driver for most Additive Manufacturing technologies is the part volume, meaning it can even reduce the production cost when creating more lightweight, complex shapes in a smart way.
We have summarised the most important advantages of AM compared to conventional manufacturing technologies below. For each advantage, you can find one application example. Further examples can be found in the courses on Metal and Polymer Technologies.
Faster Product Development & Time to Market
AM enables faster time to market
Simplified Manufacturing Processes
AM simplifies manufacturing processes
Cost-efficient Production of Small Batch Sizes
Cost-efficient for low volumes
Increased Design Freedom
Unlocks new design possibilities
Lightweight Designs
Enables lightweight designs
Functional Integration
Enables part consolidation
Performance Increase
Boosts part performance through redesign
Design features
Design freedom allows for complex designs
The increased freedom of design of most AM technologies enables the production of complex parts. Using this design freedom will ultimately lead to added functionality to your components.
Below you can find examples for parts from different industries that use design features that are unique to Additive Manufacturing.
Challenges
Challenges remain for all AM technologies
Being aware of the benefits of Additive Manufacturing is equally important as understanding its challenges and limitations. While the advances of existing technologies and new processes solve more and more of these challenges, there is no technology out there that is able to solve all of them.
We have summarized the most important challenges and limitations of AM below.
Limited Choice of Materials
Material options and data remain limited
Low Production Volumes
Lower throughput, but improving
Limited Design for AM Knowledge
Design knowledge is crucial
High Machine and Material Cost
High equipment and part costs
Lack of Standards & Certification
Lack of industry standards
Support structures
Support restricts freedom of design
Many metal Additive Manufacturing technologies require support structures that are created during the printing process to improve heat conductivity and prevent distortion of the part. The need for support structures leads to certain design and process limitations. The type, amount and even material of supports as well as the rule set to apply them greatly differ depending on the considered process.
In PBF technology, support structures are required for numerous reasons. They are placed below overhangs of parts to allow for a build-up of material on consecutive manufacturing layers. Since powder acts as a heat insulator, supports are needed to dissipate the heat from the exposed area and avoid balling of molten material. Part overhangs with an angle below 45° with respect to the building platform have to be supported. The exact angle might differ depending on the material and process parameters.
In LB-PBF the powder bed does not possess a mechanically stabilizing property, therefore support structures fix the part to the building platform to avoid undesired part movement during coating process with new powder. Furthermore, the support structures have to counteract heat-induced residual stresses and prevent deformation of a part. Similar to other welding processes, residual stresses are formed during the material fusion and solidification. For some parts it may be beneficial to use solid structures that withstand the load from residual stresses or place the parts directly onto the building platform.
To reduce the efforts of support removal and allow more complex geometries LB-PBF OEMs are working on improved process strategies to realize support free manufacturing of lower angles. Most prominently VELO 3D introduced a LB-PBF system and process concept, that significantly reduce the need for support structures. The system uses a combination of a proprietary recoating system and a software to optimize exposure. The aim is to minimize inherent stresses during the process and optimize the heat management, which results in fewer supports. Other LPBF suppliers like EOS and SLM SOLUTIONS have also introduced solutions, many based on optimized exposure strategies to build overhangs support free.
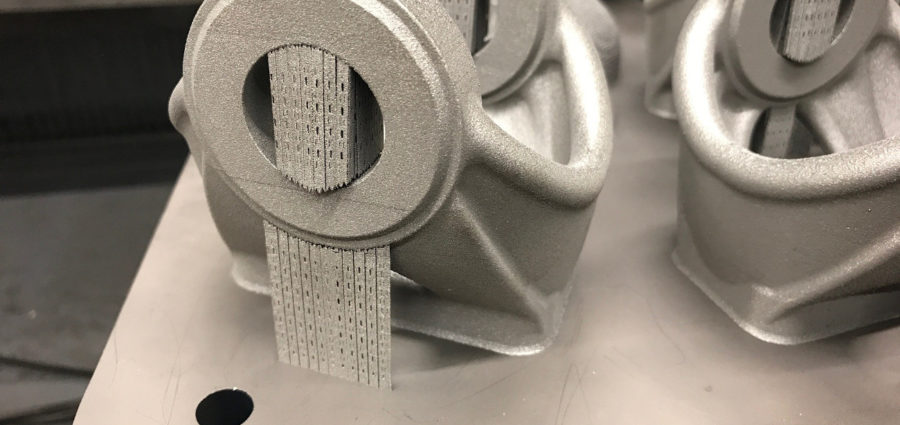
Thin and easy to remove support structure.
Solid connection of the part. Radius to prevent cracking by residual stress.
Supports broke during printing process due to residual stresses.
The supports are removed after the building processes. The respective part end of the support structure is typically tapered. High notch stresses near this part interface lead to a predetermined breaking point and facilitates the support removal. The supported surface has to be post-processed to remove support remnants. Supports should not be attached to surfaces where a subsequent machining is undesired or even impossible, such as for to lattice structures or other filigree features. Thus, the building direction and subsequent support is of a major importance during data preparation.