AM Academy
Additive Manufacturing
Online Learning
Independent Online Learning Programs for Additive Manufacturing
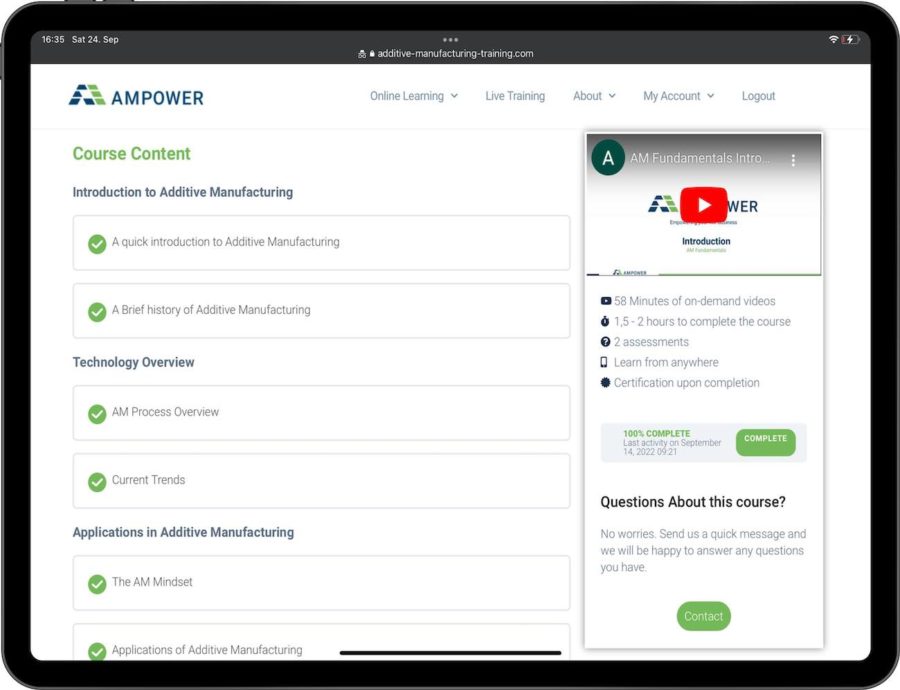
The AM Academy offers a wide range of self-paced Additive Manufacturing online learning programs. These trainings are targeted at engineers, managers and other professionals that are working with the technology on a daily basis. The online learning programs can be combined with live trainings for a hands-on implementation of Additive Manufacturing.
Additive Manufacturing Online LEarning References
What our customers say about the AMPOWER Academy
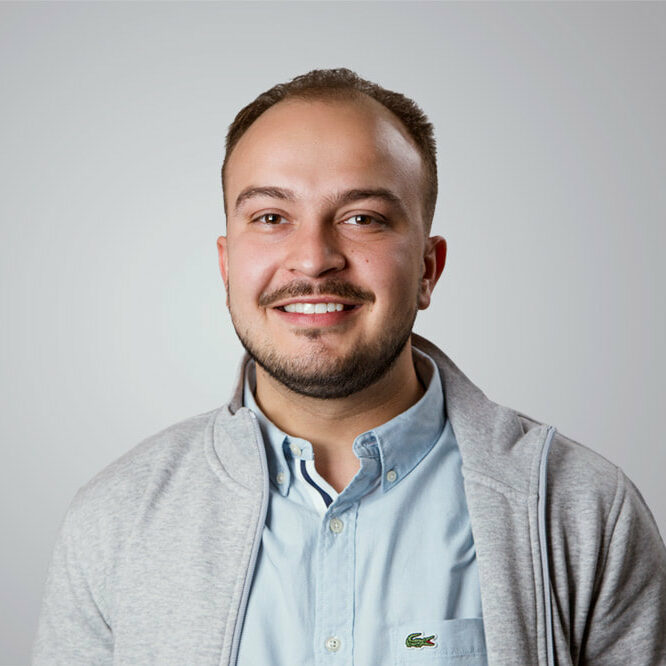
AM North
Get an overview of the AM market
The course AM FUNDAMENTALS helps you understand the most important topics to get started, such as different process categories, current trends, the AM mindset and application examples. This course is the ideal starting point for everyone that wants to get an overview of Additive Manufacturing and apply the technology on the job.
Dive deeper into metal technologies
The course METAL TECHNOLOGIES allows you to dive deeper into the different metal technologies. Besides maturity of all common metal technologies, it covers the working principle, technical characteristics, application examples and supplier landscape of the following processes:
- Laser Powder Bed Fusion
- Electron Powder Bed Fusion
- Metal Binder Jetting
- Powder Laser Deposition
- Wire Arc Additive Manufacturing
- Metal Material Extrusion
This course will enable you to select the right metal process for your applications.
Better understand polymer technologies
The course POLYMER TECHNOLOGIES enables you to confidently navigate in the polymer technology landscape. Besides maturity of all common polymer technologies, it covers the working principle, technical characteristics, application examples and supplier landscape of the following processes:
- Laser Powder Bed Fusion (LPBF)
- Material Extrusion
- Vat Polymerization
This course will enable you to select the right polymer process for your applications.
Select the most suitable applications
The online learning course PART IDENTIFICATION teaches a structured methodology that allows you identify suitable components for AM. The course covers topics such as how to evaluate the technical feasibility of an application, how to identify the value that AM can bring to a part and gives an overview of different software tools for part identification. This course is for everyone that wants to apply Additive Manufacturing to their parts.
Quickly estimate costs for metal applications
The Additive Manufacturing online learning course COST CALCULATION METAL enables you to deeply understand the cost drivers for the most common AM technologies. It covers the fundamentals of AM cost calculation and at the same time provides general values for inhouse and external manufacturing costs for the following metal technologies:
- Laser Powder Bed Fusion (LPBF)
- Electron Powder Bed Fusion (EPBF)
- Metal Binder Jetting
- Metal FDM
- Laser Metal Deposition (LMD)
- Wire Arc Additive Manufacturing (WAAM)
This course is specifically targeted towards designers and professionals that need to calculate costs for metal AM.
Get the most out of L-PBF
The Additive Manufacturing online learning course METAL L-PBF DEEP-DIVE enables you to fully understand the most mature metal technology. It covers key topics such as technology and process chain, material availability and properties as well as design guidelines and applications. This course is specifically targeted towards designers and other professionals that are working with L-PBF.
Dive deeper into the world of sinter-based Additive Manufacturing
The Additive Manufacturing online learning course Sinter-based Additive Manufacturing deep-dive enables you to fully understand technologies such as Metal Binder Jetting and Metal Material Extrusion. It covers key topics such as technology and process chain, material availability and properties as well as design guidelines and applications. This course is specifically targeted towards designers and other professionals that are working with sinter-based AM technologies.
Basic Additive Manufacturing Online Learning Courses
Metal Technologies
Understand the most important aspects related to metal AM technologies
Polymer Technologies
Understand the most important aspects related to Polymer AM technologies
Advanced Additive Manufacturing Online Learning Courses
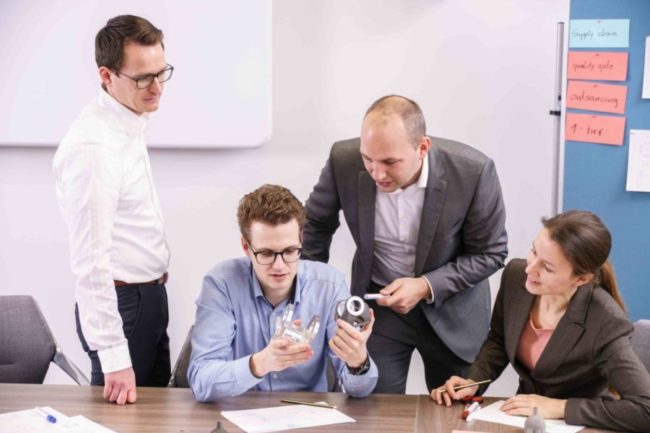
Additive Manufacturing Online Learning Teaching styles
Combination of online learning with live courses
Each online learning course consists of a mixture of videos, interactive content and further reading material. The videos last few minutes each and summarize the most important content. Besides, you can click through the content with more details and external links. A quiz at the end of each course tests your knowledge. Every course comes with a pdf summarizing the content as well as further reading materials to dive deeper into the topics.
The AMPOWER online learning programs can be complemented by live courses that are held by AMPOWER employees or experts from our network. The online learning programs generally form a basis for a more hands-on and in-depth discussion during a live course. Live courses can take place online or at customer facilities.
Additive Manufacturing Online Learning Certificate and Tests
Ensure progress through tests and certificates
At the end of each course, a quiz assessing the most important content ensures that all relevant points have been understood. Each quiz consists of different question types such as True or False, Multiple Choice or visual sorting questions. Members receive a certificate for the successful completion of each course awarded by AMPOWER. Certificates are a great way to keep track of which employee has earned what type of skills.
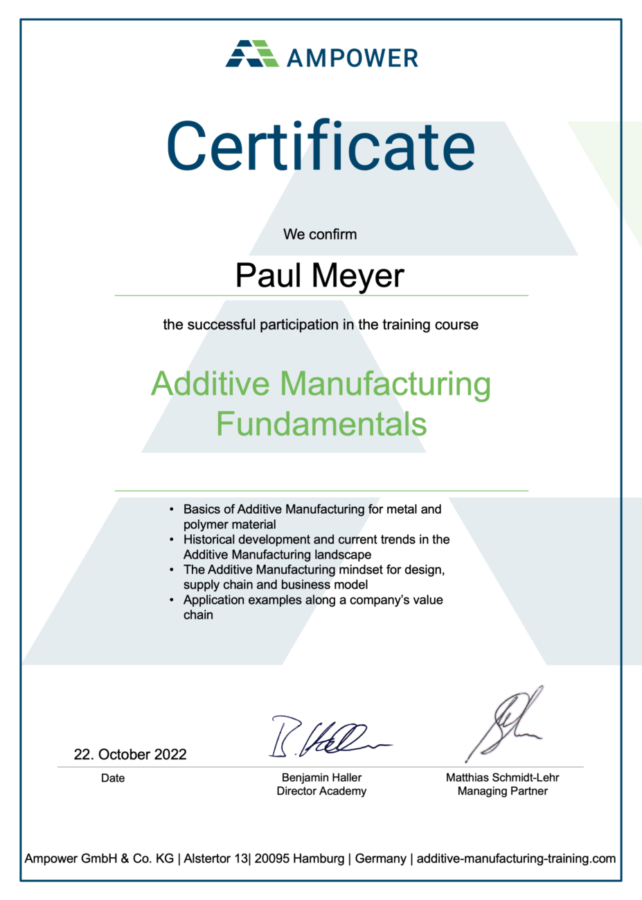
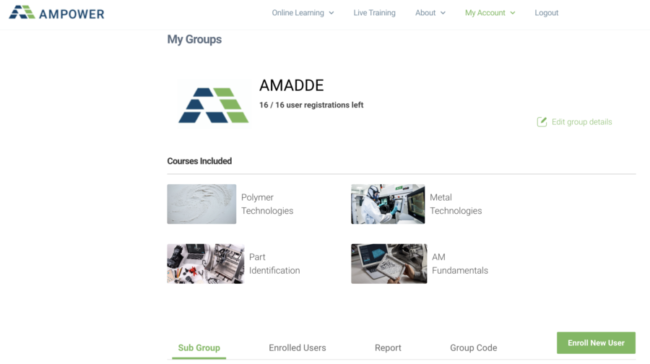
Additive Manufacturing Online Learning Team Functionalities
Create a group for your company, add team members and monitor their progress
Purchasing a team license allows you to create a group where you can add colleagues and monitor their progress as well as view their test results. Simply create a group code and share it with your colleagues so they will automatically join your group.
Additionally, company-wide access can be set up in order to train an unlimited number of employees across different sites.
Additive Manufacturing Online Learning Trial Course
Subscribe to start free trial
You can access the first course Additive Manufacturing Fundamentals for free after subscribing to the AMPOWER Academy newsletter.
Understand the most important topics to get started with Additive Manufacturing