Maturity of metal processes
Race of the technologies
Metal Additive Manufacturing is often associated with Laser or Electron Beam Powder Bed Fusion process. However, there are more than 18 different technology principles identified today. While some of these principles are in an early development stage, many are successfully used in industrial set-ups or it is expected that they will find a viable niche as manufacturing technology.
To be successful in using metal Additive Manufacturing, it is highly important to choose the right established or new manufacturing technology. Therefore, this chapter provides an overview on upcoming technology principles and assesses their potential.
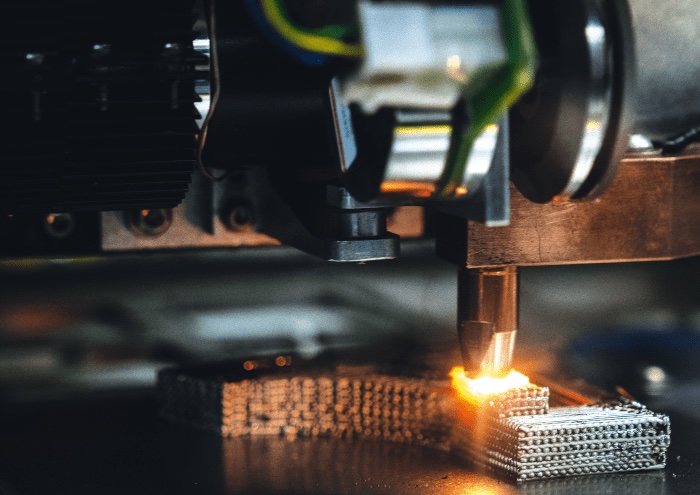
What you will find in this section
Industrialization and Technology Maturity Index
Evaluation with maturity index
To evaluate the different AM technologies AMPOWER has developed a model to characterize the maturity of an Additive Manufacturing technology based on two indices. The Industrialization Maturity Index and the Technology Maturity Index describe and compare the capabilities and adoption rate of each AM technology in the industrial environment. Both indices are crucial factors for evaluating the current status of any AM technology.
- The Technology Maturity Index evaluates the process capability, system reliability and availability as well as implemented quality control measures.
- The Industrialization Index assesses the supply chain, material availability, installed system base, public knowledge and research as well as standardization of each technology.
Each category is weighted according to its specific importance. Typically, the technological maturity increases first, and the industrialization follows. A detailed description of the current state of maturity is given in the deep dive section for each technology.
Technologies with AM Maturity Index “Prototype system” are still at an early development stage with in-house systems only or on the verge of first systems at beta-customers. Many of the technologies in this corridor are proprietary AM principles or just recently made public.
At a Maturity Index of “First application”, industrial adoption takes place and users introduce the technology in their R&D departments or machines are set up for pre serial production trials at beta-customers.
Technologies at a Maturity Index of “Industrial use” are on the verge of full industrialization. Technologies in this area have not yet been widely adopted as a serial manufacturing technology across multiple industries.
To reach “Widespread industrial use” the technology must be established in multiple industries as a production technology for functional end parts.
Due the industrial focus, AMPOWER does not rate technologies that are still in the proof-of-concept stage.
Laser Powder Bed Fusion
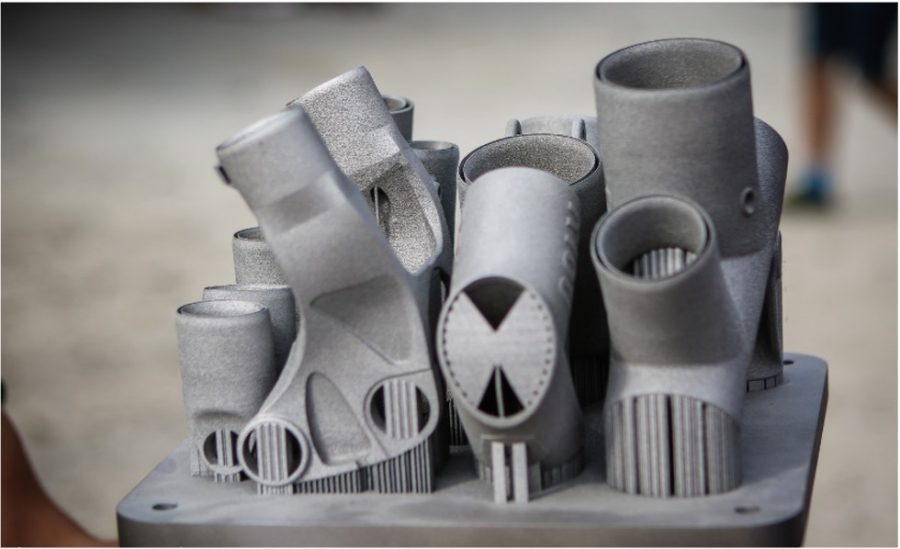
Technology Maturity Index: Very High
Industrialization Maturity Index: Very High
Laser Beam Powder Bed Fusion still holds the top spot in technological maturity as well as in industry wide adoption. The use of L-PBF for the production of end parts in highly demanding industries such as medical, aviation and the energy sector has driven a continuous improvement of machine hardware and process reliability over the past five years.
2022 has been another very successful year for Chinese L-PBF machine manufacturers. With their strong domestic positioning bolstering their sales volumes, the Chinese manufacturers slowly push onto the Western markets. Currently mainly smaller machines for dental and industrial applications are installed in Eastern Europe, but the continuous development and improvements of machine technology enable them to compete with Western suppliers. At FORMNEXT 2022 all major Chinese suppliers displayed their large and multi-laser platforms and the first Western European service suppliers have installed multi-laser large format from E-PLUS and FARSOON, emphasizing that these systems can compete on reliability and quality.
The trend of ever more increasing build chambers continued last year. Driven by large size applications from the space, turbine and energy industry as well as economy of scales in systems with 8+ lasers, SLM SOLUTIONS and VELO increased their sales volume of very large machines significantly. And with new machine release from Chinese manufacturers the number of very large (600+ mm) L-PBF system suppliers increases continuously. Currently, E-PLUS is taking the lead in size with their 2022 release of the EP-M 1250 that comprises a build chamber of 1250×1250 mm and 9 lasers. Parallel to these developments all major machine OEMs are continuously and incrementally improving their machine reliability and user friendliness.
In last year’s AMPOWER Report issue Area-wise Laser Powder Bed Fusion was introduced to the AMPOWER Maturity Index. The proprietary process from SEURAT TECHNOLOGIES uses a high power, pulsed laser source as well as complex optics to melt complete areas in one shot. The process mirrors the principle of Area-wise Vat Polymerization and therefore promises extremely high productivity. Since its introduction the technology only marginally increased in its Industrialization Index, with first customers able to order parts. Further developments to reach maximal pulse rate and laser power are still ongoing and become increasingly difficult, if the projected melting rates want to be achieved. Due to the complexity and extremely high investment cost of the high-power laser source and especially the needed optical components it is most likely, that the technology will be used for part production only without external machine sales for the foreseeable future.
Electron Beam Powder Bed Fusion
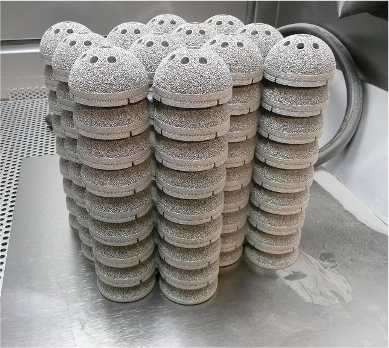
Technology Maturity Index: Very High
Industrialization Maturity Index: Very High
Electron Beam Powder Bed Fusion follows L-PBF to reach “wide-spread industrial use” in 2022. The continuously growing number of machine OEMs over the last few years advance the technological capabilities as well as the targeted applications. Besides long-established production in the medical and aviation industry, E-PBF is increasingly used in oil and gas, space and industrial applications. The machine concepts from the new market entries combine the E‑PBF advantages of high productivity and stress-free production with typical Laser PBF properties of free-flowing powder and high resolution. Furthermore, they focus on high speed serial production system with interchangeable build modules, similar to designs we see in the larger production-focused L-PBF machines.
Directed Energy Deposition
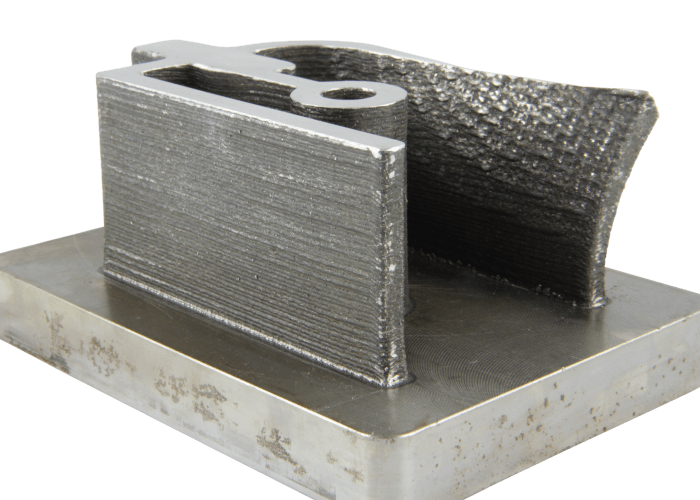
Technology Maturity Index: Very High
Industrialization Maturity Index: High
Powder Laser Energy Deposition technologies did not see a significant repositioning in the Maturity Index over the last year. With its high technology maturity and established supplier landscape Powder Laser ED has established itself for very specific applications. Mostly used in repair and rebuilding of worn high-cost parts, e.g. turbine blade tips, the technology struggles to identify further non-coating business cases across multiple industries. After fast progression in maturity over the last years, Wire Laser Energy Deposition had reached the level of “Industrial use” in 2021. Since then, the progress slowed down significantly and at the moment the suppliers and users are focused on finding its application sweet spot between Powder Laser and Wire Arc ED technologies. Given the availability of turn-key solutions from companies such as MELTIO and MITSUBISHI ELECTRIC, as well as several process head and machine integrators offering Wire Laser technology, further progress in this field is highly probable in the coming years.
Last year both Wire Arc technologies have made the biggest jump in the Maturity Index. Particularly the publication of multiple standards in the maritime and oil and gas sector helped increase the Industrialization Index of Wire Electric Arc Energy Deposition in 2022. Additionally, the strong competition and the high market dynamics between software driven start-ups like MX3D on one side and established welding equipment OEMs like LINCOLN ELECTRIC on the other have fostered the success of Wire Electric Arc technologies. Similarly, Wire Plasma Arc Energy Deposition has completed final qualification hurdles for civil aviation in 2022. This success combined with the increasing demand for sustainability and resource efficiency will further establish Wire Plasma Arc as a manufacturing technology of high value metal blank from titanium and nickel alloys.
Material Extrusion
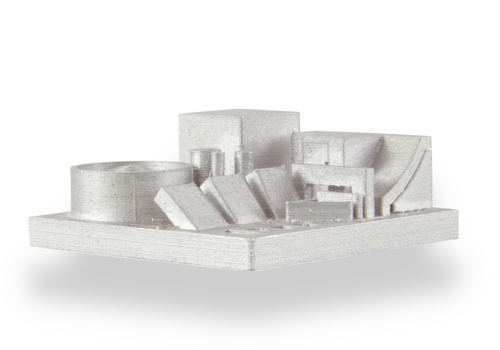
Technology Maturity Index: High
Industrialization Maturity Index: High
Metal Filament Material Extrusion and Metal Pellet Material Extrusion did not mature significantly over the last year. Both technologies suffer from the knowledge and investment intensive post processes of debinding and sintering. Difficult to assess shrinkage and likely deformation during the sinter process require extensive knowhow and simulation capabilities to achieve first time right metallic parts. The currently employed trial and error approach runs contrary to the promise of fast and efficient low volume part production. Today the sales of Metal Filament Material Extrusion are mostly into Academia and R&D departments to evaluate the technology for tool or one-of part production. Metal Pellet Material Extrusion lacks significant sales volumes due to limited machine availability and reliability. The promise of extremely cheap, readily available feedstock might help the technology to progress in real industrial applications, but only if the complete process chain from design and simulation until sintering is easily controlled. Both technologies, however, face increasing competition from low-cost L-PBF systems and therefore will most likely have to focus on tool applications and materials only able to be process by sintering.
Binder Jetting
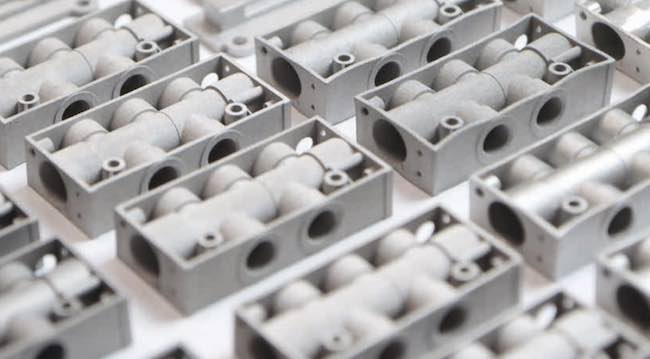
Technology Maturity Index: High
Industrialization Maturity Index: High
Binder Jetting reached the state of “industrial use” in 2022. The technology benefits from the large development efforts of HP, GE ADDITIVE and DESKTOP METAL to push the productivity and repeatability of the process. Main developments in 2022 were the market entry of GE ADDITIVE as well as MARKFORGED acquiring DIGITAL METAL. With the acquisition MARKFORED will broaden its sinter-based technology portfolio in addition to its Metal Filament ME technology. Tier 1 sinter suppliers such as GKN, CUMMINS and INDO-MIM are slowly increasing their production capabilities and capacities in BJT, however, are still struggling to roll out the technology on a wider industrial basis. It will be interesting to see how fast BJT will be able to overcome these hurdles and follow LPBF and E-PBF into ”widespread industrial use”.
The technology Hybrid Binder Jetting combines binder application for solidification and a mechanical spool for contouring of the green parts. 3DEO the inventor of the proprietary technology focusses its business model on part manufacturing rather than machine sales. With their currently very concentrated approach on stainless materials the progress in the Industrialization Index is steady but slowly, although the technological maturity is quite advanced and on par with Binder Jetting.
Cold Spray
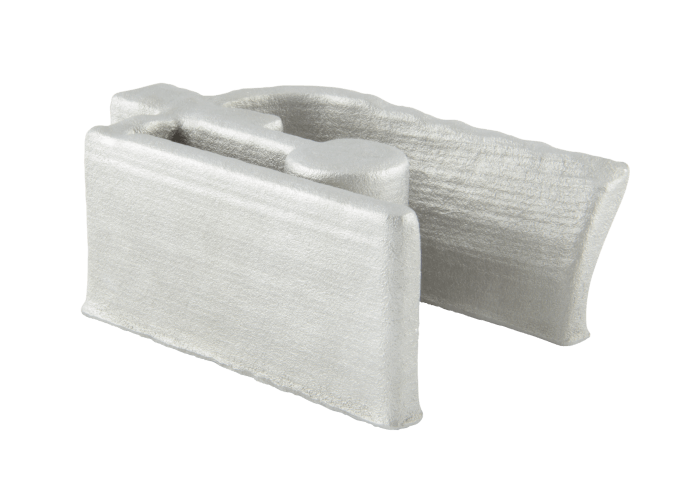
Technology Maturity Index: Medium
Industrialization Maturity Index: Medium
Cold Spray Additive Manufacturing advances slowly in its technological and industrial maturity. With only a handful of machine suppliers the technology struggles to identify new industrial applications beyond blank production and on-site spare part supply. Besides SPEED3D, companies such as TITOMIC try to establish Cold Spray Additive Manufacturing as an inexpensive and fast way to create near-net shape parts but are challenged by the limited design freedom. HERMLE focusses its Cold Spray ambitions completely on the production of large molds using their unique approach of hybrid manufacturing in combining Cold Spray and machining in one machine. Furthermore, they utilize water soluble material to create cooling chancels in the part. Most likely, the technology will settle in a niche AM existence with few specific applications.
Mold Slurry Deposition and Metal SLS
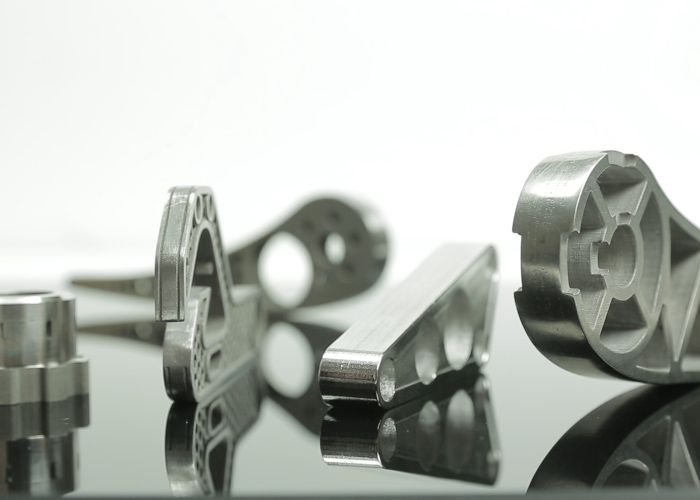
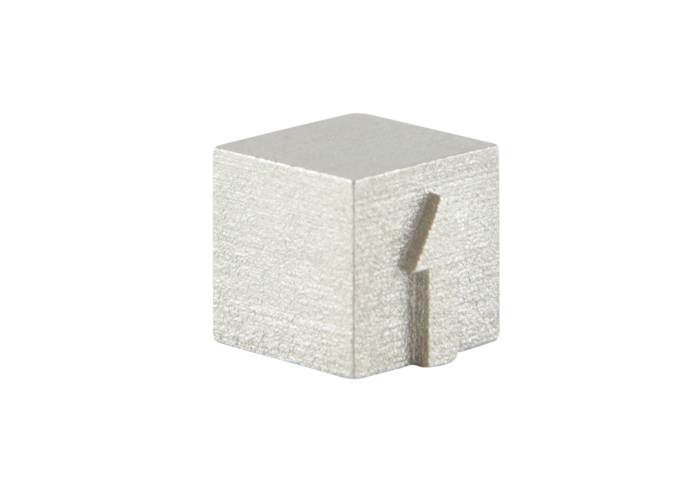
Technology Maturity Index: Medium
Industrialization Maturity Index: Medium
After fast progressions in the last two years Mold Slurry Deposition and Metal SLS are currently set in their positions in the Maturity Index. Both sinter-based technologies have found first customers and applications. This status might not change quickly over the next few years. Due to the proprietary nature of both technologies, potential customers might tend to favor competing technologies with multi-sourcing options and larger public research efforts such as Binder Jetting.
Liquid Metal Printing
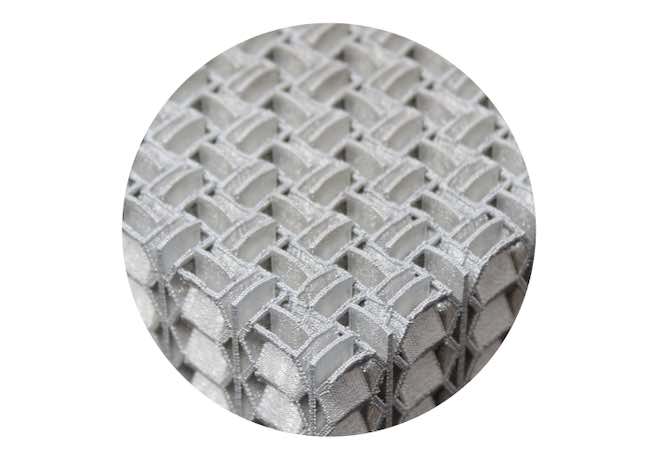
Technology Maturity Index: Medium
Industrialization Maturity Index: Medium
Liquid Metal Printing experienced a major setback in 2022 and therefore was not able to further advance in the Maturity Index. XEROX one of the leading technology providers discontinued its operation and halted all its R&D and sales activities. Fortunately, GROB-WERKE displayed its newly developed machine at Formnext 2022 to fill the gap XEROX is leaving. As an established CNC machine builder and manufacturing solutions provider in the automotive industry, GROB-WERKE aims to establish the technology for low volume castings and spare parts. The current and foreseeable limitations to low melting alloys will most likely prevent a wider spread industrial use in the foreseeable future.
Metal Lithography and Nano Particle Jetting
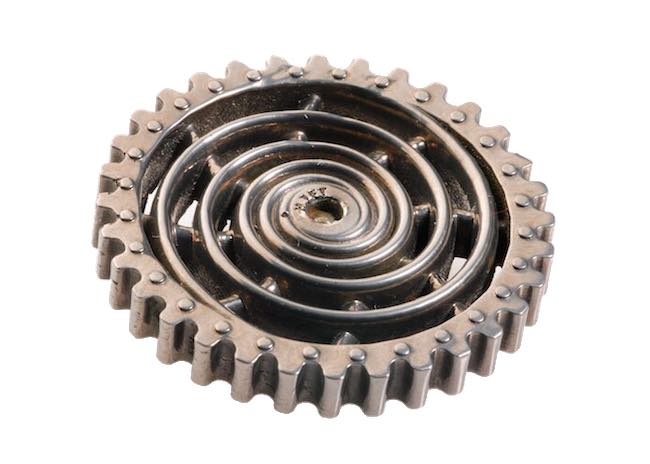
Technology Maturity Index: Medium
Industrialization Maturity Index: Medium
Metal Lithography and Nano Particle Jetting did not advance significantly over the last 12 months. Both technologies use a two-step process of 3D printing the green body and densifying the metal material in a final sintering step. While Metal Lithography creates the single layers in a liquid bed, Nano Particle Jetting creates the parts with direct droplet printing. Both technologies achieve very high resolutions and focus on small part applications. The strong focus on very small parts and lengthy technology development to create a robust process chain from start to finish have made it difficult to find many industrial applications. However, with a growing number of machine suppliers and the shipment of first machines to customers these technologies might find future applications in the medical, jewelry and electronics industry.
Friction Energy Deposition
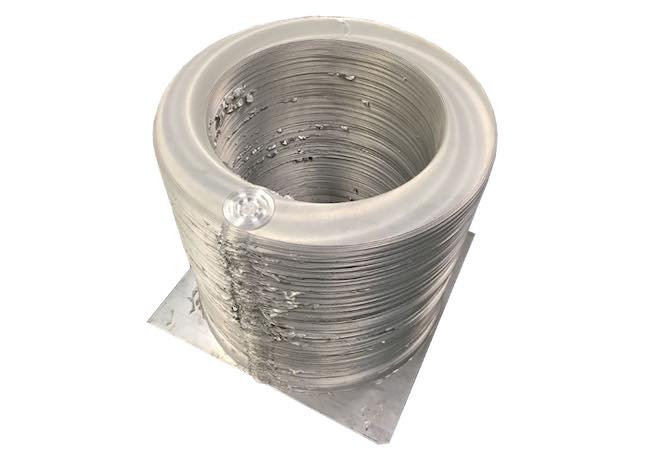
Technology Maturity Index: Medium
Industrialization Maturity Index: Medium
Friction Energy Deposition advanced in the Maturity Index in 2022. Since the technology is promoted by only a few machine suppliers it struggles to penetrate the AM and general technology market. Nonetheless, MELD was able to progress the technology and “win” first applications in the defense industry. Additionally, MELD launched its own part production service in 2023 to serve additional applications and industries with parts from its Friction Energy Deposition Technology.