Design to cost
Optimize the part design with cost in mind
Design to cost (DTC) is a product design approach that focuses on designing a product within a predetermined cost target. Design to cost in L-PBF design requires a thorough understanding of the cost drivers of the process, including material costs, machine time, and post-processing. The goal is to optimize the design for L-PBF while ensuring that it remains within the cost target.
To achieve DTC in LPBF design, designers may use various strategies, such as reducing the part’s complexity to minimize material usage and build time, optimizing the part’s orientation to reduce support structures and minimize build time, and designing the part with post-processing requirements in mind to minimize the amount of post-processing needed.
What you will find in this section
Minimize build volume
Printing time is main cost driver in producing AM “raw” part
The printing time is the main cost driver in producing the AM raw part. Since the printing time is directly linked to the volume of a part, reducing the overall part volume is the most important thing to keep in mind when designing for cost. Every AM optimized part should be reduced to its minimal necessary material volume. Besides printing time, this also saves material.
Creating designs with minimum volume might be specifically hard for designers that are used to design for conventional technologies such as milling. Since these processes start from a massive block and then mill away material to reduce weight, complex lightweight designs usually lead to more machining operations and thus higher costs.
For AM, minimizing the build volume can typically achieved by printing thin-walled parts or hollow structures. If necessary, lattice structures can be introduced to add additional strength.
Minimize and ease post processing
Post processing accounts for up to 50% of total production costs

Post processing can be a major cost driver for the finished component and can account for up to 50% of the total production costs. Since the removal of support structures usually still is a manual process, it is important to avoid them as much as possible. Whenever necessary, they should be designed in a way that they can easily be removed.
In addition to support removal, AM-specific designs often require complex milling processes. Machining tolerances, mounting surfaced and references should be planned in every AM design and in the best case directly discussed with the machining company. Since the surface roughness and accuracy varies depending on the orientation in the printer, some post processing operations might be possible to avoid when selecting a smart orientation in the printer.
Increase packing density
Increase packing density to reduce cost
A higher job utilization reduces the part costs significantly. The graph on the right displays the cost per volume depending on the job volume and job height. The job volume is calculated by adding up the volume of all parts that are printed in one build job. With increasing job volume, unproductive times such as machine set-up or layering time are distributed over a higher number of parts and the cost per volume decreases. The two lines show that with an equal job volume, a greater job height will lead to higher cost per volume. The reason is that the higher build job will require more layers and thus additional build time and cost. Once a certain job volume is reached the cost per volume does not decrease significantly anymore.
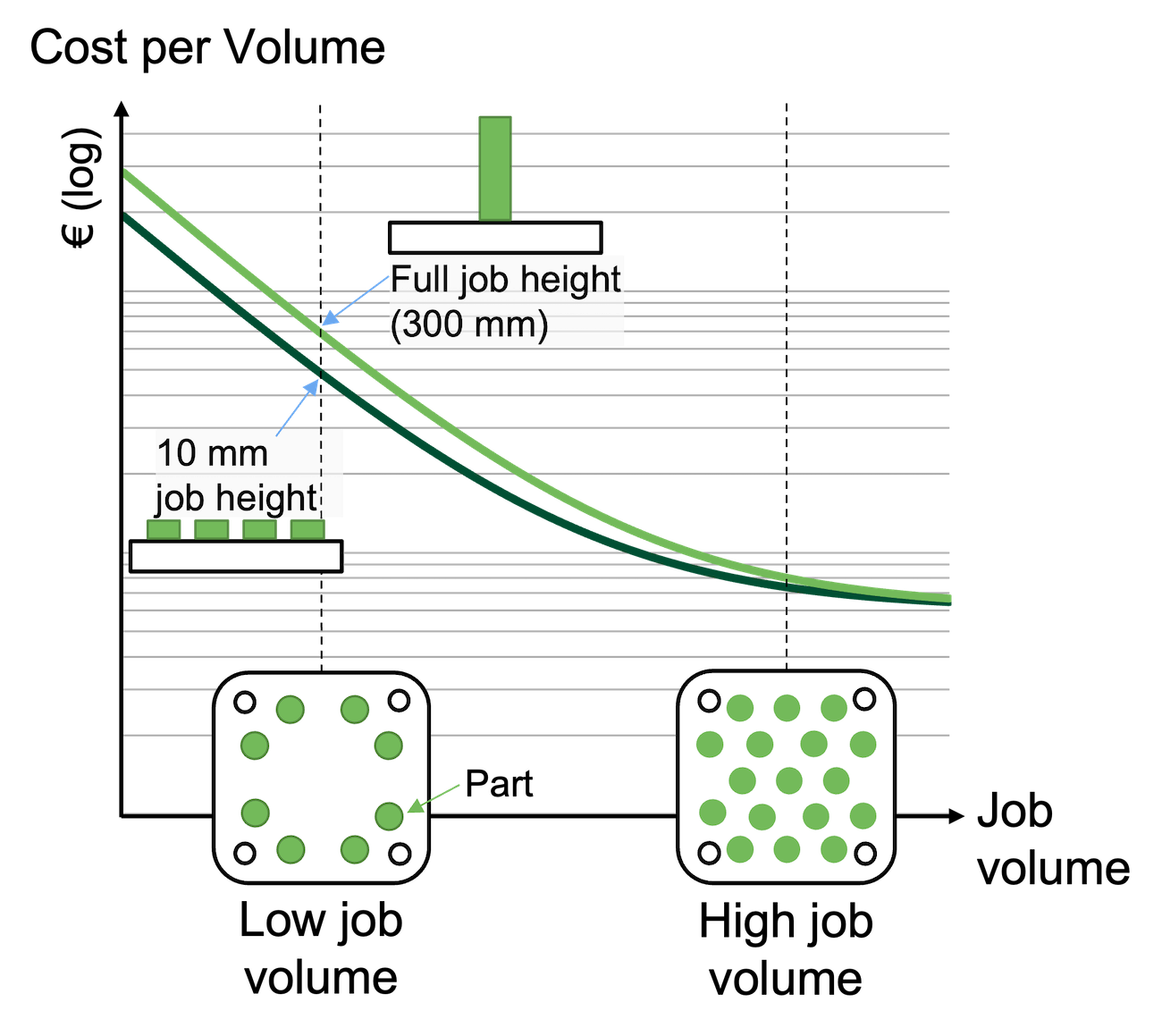