Process deep-dive
Over 100 process parameters to influence the final part properties
The L-PBF process allows users to control and change approximately 100 process parameters that all have an influence on the final part quality. The fact that these parameters influence each other makes selecting the right parameter complex. The graph displays some of the most important influencing factors of the L-PBF process. We separate them into actuating variables and noise variables. Actuating variables are used to actively influence the melting process and are typically adjusted when developing or optimizing a parameter for a new material. Noise variables, on the other hand, also have an influence on the part quality but are rather controlled to keep a constant result..
In this section we will focus on the process parameters that are typically adjusted to optimizing the melting of a new material. These parameters are typically expressed in a resulting Volumetric Energy Density (VED), which is defined as
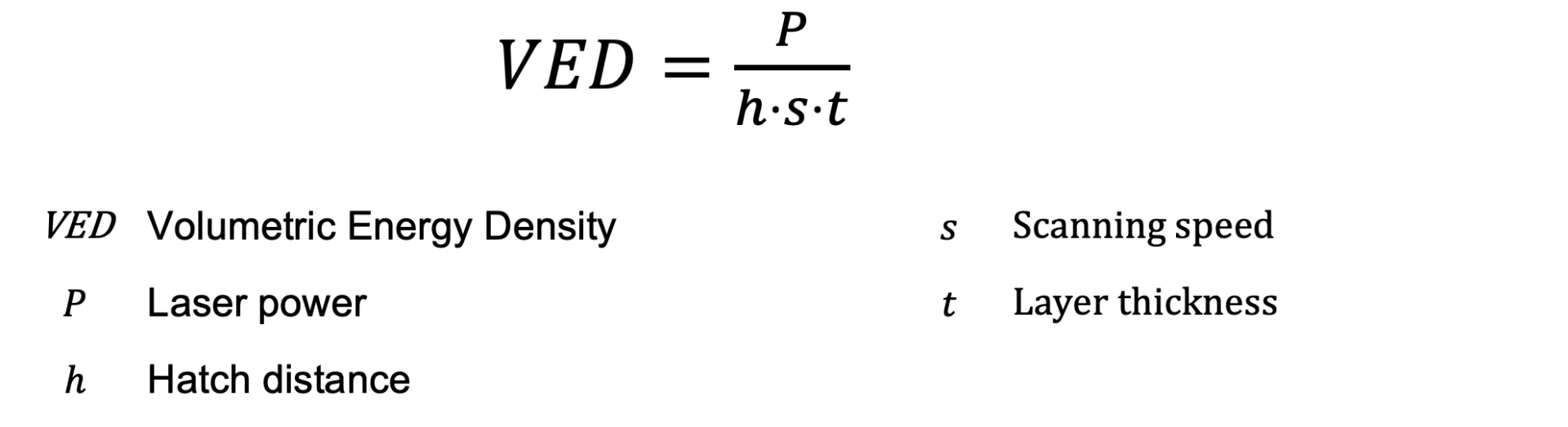
What you will find in this section
Laser power
Laser power to define meltpool size and productivity
The laser power affects the melting and solidification behavior of the metal powder, as higher power will result in a larger melt pool and a deeper penetration depth. It can also affect the cooling rate of the melted metal, leading to changes in the microstructure and mechanical properties of the final part. Larger melt pools can be advantageous for larger parts or thicker layers, but can also lead to thermal distortion and reduced resolution.
The image shows a schematic illustration of the melt pool during the L-PBF process. The melt pool dynamics are crucial to the overall quality and mechanical properties of the final product. The dynamics refer to the physical and thermal processes that occur within the melt pool, such as fluid flow, solidification, and heat transfer.
The temperature in the melt pool can reach up to several thousand degrees Celsius, and the cooling rate can be extremely high, leading to complex thermal gradients and solidification patterns. The speed and direction of the laser beam, the laser power, and the material properties all affect the melt pool dynamics.
The melt pool dynamics can also affect the microstructure and mechanical properties of the final product. For example, if the cooling rate is too high, it can cause cracking and residual stresses in the material. On the other hand, if the cooling rate is too low, it can lead to the formation of defects such as pores and inclusions.
Scan speed
Scan speed in combination with laser power the most important factor
The combination of scan speed and laser power is the most important parameter combination for a robust welding process. Selecting the right combination will lead to a continuous and stable weld seam, minimized spatter and an increased productivity.The energy density, which is defined as laser power divided by the spot area, is typically the first factor that needs to be considered when developing a new parameter for a given material.
The picture on the left shows that when reducing the energy density, the weld seam first turns into a discontinuous melting track and finally results in single droplets on the right side. This so called balling effect will ultimately lead to defects such as porosity, micro cracks or poor surface finish.
The right picture shows the surface of 3 cubes that were produced in the same material with different energy densities. The cube in the middle, which was produced with a VED of 1.28, shows an even microstructure. The laser lines are still visible and were following a so-called “chessboard” scanning strategy that is often used to increase temperature homogeneity. The cube on the left, which was build with an equal laser power of 200W but a lower scan speed of 200 mm/s had a too high VED of 2.38.
The cube on the right was built with a laser powder of 200W and a scan speed of 2 500 mm/s and thus a too low VED of 0,66. This led to a lack of fusion and ultimately a rough surface and high porosity.
Layer thickness
Layer thickness as the most effective way to increase productivity
The layer thickness is the most effective way to increase productivity in the LPBF process. Doubling the layer thickness will cut the print time nearly in half and thus has a huge impact on the cost per part. Besides productivity, another positive effect are typically less residual stresses. On the downside, a higher layer thickness typically also comes with an increased surface roughness and a lower detail accuracy. The effect on the mechanical properties is complex and cannot generally be defined.
Residual stresses
Residual stresses as the main risk during the LPBF process
Residual stresses are stresses that remain in a material even after the external loads or thermal loads have been removed. In the context of the L-PBF process, residual stresses can be generated due to the complex thermal interactions that occur during the process.
During the L-PBF process, the material is heated and melted by the laser and then rapidly cooled and solidified, which can create temperature gradients and thermal stresses. Additionally, the successive layers of material can induce thermal expansion and contraction, leading to additional residual stresses. These residual stresses can affect the dimensional accuracy, mechanical properties, and fatigue behavior of the final product.
The magnitude and distribution of the residual stresses in L-PBF depend on various factors, such as the laser power, scanning speed, layer thickness, material properties, and the cooling rate.
To mitigate the impact of residual stresses on the final product, various strategies can be employed such as post processing treatments (e.g., heat treatment, shot peening) to relieve the stresses, optimizing the process parameters to reduce the stress generation, and improving the design of the product to reduce stress concentrations.
Another strategy to lower residual stresses that is often used is to preheat the powder during the build process. This will both decrease the temperature gradient and also lower the cooling speed. Most industrial systems today are equipped with based plate heating capabilities of around 200°C and first systems come up that use different strategies to heat up the powder to even higher temperatures.
Scan strategy
Scan strategy with a great potential to further reduce residual stresses
The scan strategy refers to the pattern and direction of laser scanning during the L-PBF process. The graphic on the left displays some common scan strategies that are used to melt the material.
The arrows depict one laser vector. These strategies have partially been deducted from the welding process. The goal of the scan strategy is to achieve a homogenous temperature distribution, ultimately leading to the a stress reduction. Optimizing the scan strategy becomes more complex for multi-laser machines. It must be noted that scan strategies are often known under various synonyms, e.g. paintbrush scanning is often also referred to as stripe scanning.
More recently, several machine suppliers such as VELO3D, SLM SOLUTIONS, and EOS released process parameters to reduce the need for support structures. This can be achieved by editing process parameters such as laser power, scan speed, hatch distance to generate a different downskin energy.
Gas flow
Gas flow with a big impact on process stability
The gas flow is another important factor on the melting process. The goal is to create a homogenous, lamellar gas flow to ensure a stable welding process. The gas flow fulfils several functions: First it is used to constantly transport away the spatter and smoke that occurs during the melting process. Second, it is used to protect the shielding glass and optical system. An inhomogeneous gas flow shows a large influence on the material quality and will lead to increased porosity and surface roughness.
Beam Shaping
Advancing productivity and material control
Beam shaping is a critical innovation in Laser Powder Bed Fusion (L-PBF) technology, addressing challenges like build speed, material quality, and production costs. All-fiber beam shaping, as exemplified by nLIGHT’s AFX fiber lasers, allows precise control of beam profiles. These profiles include single-mode Gaussian beams for fine details and ring or saddle-shaped beams for larger features, offering flexibility to match specific manufacturing needs.
This demonstrates how laser beam profiles influence the thermal dynamics in the melt pool, affecting material density, microstructure, and process stability. Shaped beams reduce spatter and improve consistency, enabling faster build rates—up to 7.8 times faster in some studies—and reducing part costs by as much as 60%.
This also brings the potential to engineer material properties within a single part. By manipulating thermal gradients and grain structures, manufacturers can achieve components with tailored mechanical properties, such as variable stiffness or strength. This approach illustrates how beam shaping can push the boundaries of traditional manufacturing, emphasizing its role in advancing L-PBF for industrial-scale applications.