How to choose the right metal technology
Typically more than one suitable technology for each application
Choosing the right technology can be tricky. Selecting the right process always depends on your application and its requirements. Before presenting an overview of typical characteristics of the different technologies covered in this online learning program, we will present 2 common selection criteria: part dimensions and productivity.
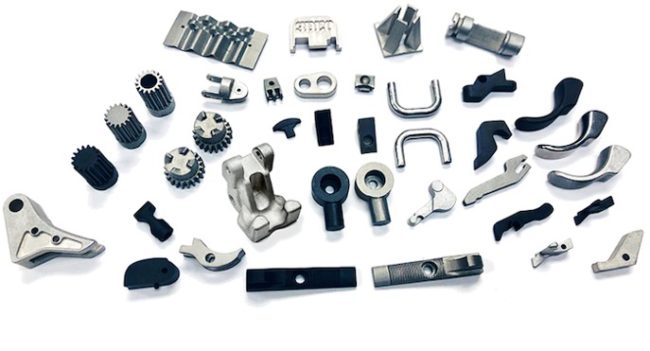
What you will find in this section
Part dimensions
Part size is a simple first indication to narrow down possible technologies
One of the most common selection criteria for metal processes are part dimensions:
- Material Extrusion and Binder Jetting are mostly suitable for small components. Here the limitation results from the fragility of the green body and shrinkage during sintering.
- L-PBF and E-PBF can be used for small to medium-sized components. Standard industrial machines reach up to 400 mm in each dimensions, with few machines coming up reaching up to 1m in size.
- DED technologies such as Powder and Wire Energy Deposition and can be used for medium and large components. Parts can reach dimensions up to several meters and are mainly limited by machine design.
In general, the lower limit of part dimensions is restricted by the process itself. Fine features in the range of a tenth of a millimeter can be manufactured by L-PBF, where the resolution is in the dimension of the diameter of the laser spot. In Binder Jetting, high resolution printing heads and small powder particle distribution facilitates building fine features. In general, powder-based technologies have higher resolution than rod or wire-based technologies.
Productivity versus accuracy
Higher productivity often comes at the expense of lower accuracy
Metal AM technologies differ greatly in their productivity and accuracy. An increase in productivity often results in a decrease in accuracy and resolution of the process.
While the specific application and processing parameters significantly influence build speed, a simplified comparison of productivity can be made by considering the build-up rate of volume per time (cm³/h).
In L-PBF, productivity is primarily driven by the volume of material a laser melts per time interval. For certain materials, such as titanium alloys, physical limitations in melting speed already constrain productivity at today’s laser power levels. To overcome these constraints, recent advancements have focused on increasing the number of laser beam sources in machines. Modern multi-laser systems, equipped with 4, 8, or even more lasers, have drastically increased productivity, enabling build rates of over 100 cm³/h for certain materials. Simultaneously, advancements in machine architecture allow significantly larger build volumes, making these machines suitable for producing large parts or batch production of smaller components.
For layer heights around 50 µm, a single laser melts titanium or stainless steel powder at rates of 10–20 cm³/h and aluminum alloys at rates of 20–30 cm³/h. Increasing layer height can further improve these figures but often compromises resolution and surface quality. However, multi-laser systems effectively address these trade-offs by distributing the workload across multiple lasers, reducing build times without compromising accuracy or surface quality as significantly.
Non-productive times, such as recoating layers or taking quality assurance images, remain a limiting factor and can still constitute over 25% of the total process time. However, newer machines increasingly feature optimized recoating mechanisms and real-time monitoring systems that minimize these delays, further enhancing overall productivity.
The productivity of Binder Jetting (BJ) is driven by the coating and printing head’s speed across the powder layer. Announced BJ machines from DESKTOP METAL and HP incorporate single-pass coating and printing, processing the full width of the build envelope in one motion. This innovation makes productivity dependent on the packing density of parts in the build chamber—higher densities result in greater productivity while maintaining constant accuracy. Claimed green body printing rates reach several thousand cm³/h, but independent confirmation of such speeds remains limited. Depowdering and sintering times also significantly impact overall productivity.
In Material Extrusion (ME), the application rate is constrained by nozzle diameter and, for filament systems, by the speed at which the metal filament can be handled. Fragile filaments risk breaking at higher speeds, halting the process. Current build-up rates are around 15 cm³/h, but pellet-based systems offer potential for improved performance.
For Directed Energy Deposition (DED), productivity varies with system design, part geometry, and processing parameters. Cooling phases, influenced by part geometry, can consume up to 50% or more of total build time, negatively affecting productivity.
In Powder Laser Energy Deposition, nozzle diameter influences resolution and productivity, with rates ranging from 50 to 500 cm³/h. Wire Electric or Plasma Arc processes achieve build-up rates of 100 to 800 cm³/h, though with reduced accuracy compared to powder-based methods. For Wire Electric Arc Energy Deposition and Coldspray, rates can exceed 1,000 cm³/h, making them suitable for applications requiring high material deposition rather than fine precision.
Technology comparison
How do the different metal technologies compare?
We therefore created an overview of the main metal technologies below that will help you choose the right technology for your needs. You can dive deeper into the different metal technologies at the bottom of this page.
Keep in mind that the values given below should only provide you a general rule of thumb – within each technology the exact values will differ depending on machine and material.
ME
BJT
L-PBF
E-PBF
LMD
WAAM
Process Category
Extrusion
Binder Jetting
Powder Bed Fusion
Directed Energy Deposition
Typical Part size
15-250 mm
5-100 mm
15-300 mm
20-300 mm
100-1000 mm
0.2-2 m
Typical Productivity
5-50 cm³/h
10-1000 cm³/h
10-30 cm³/h (per laser)
15-50 cm³/h
50-500 cm³/h
100 -1000 cm³/h
Supports
Needed to print, debind & sinter
Not needed, may improve sinter
Usually required for low angles
Typically not needed
Typically not needed
Surface Roughness
Ra 5-20 µm
Ra 3-5 µm
Ra 5-10 µm
Ra 15-25 µm
Ra 20-175 µm
Waviness >1 mm
Typical layer thickness
0.05-0.5 mm
50-120 µm
25-90 µm
~50 µm
0.1-1.5 mm
~3 mm
How to get started
Usually more than one process for your application
The above table should provide you a general guideline how to get started selecting the right process. Keep in mind that often there is more than one process for your application. There are different databases, such as the SENVOL Database of Industrial AM machines and materials or the ANIWAA AM marketplace. These databases will allow you to narrow down the list of possible machines or materials by applying filters such as your material category, part dimensions or required part properties.
Once you have one or several technologies in mind, the next step is to reach out to an AM expert to discuss this in more detail.