Maturity of metal processes
Race of the technologies
Metal Additive Manufacturing is often associated with Laser or Electron Beam Powder Bed Fusion process. However, there are more than 18 different technology principles identified today. While some of these principles are in an early development stage, many are successfully used in industrial set-ups or it is expected that they will find a viable niche as manufacturing technology.
To be successful in using metal Additive Manufacturing, it is highly important to choose the right established or new manufacturing technology. Therefore, this chapter provides an overview on upcoming technology principles and assesses their potential.
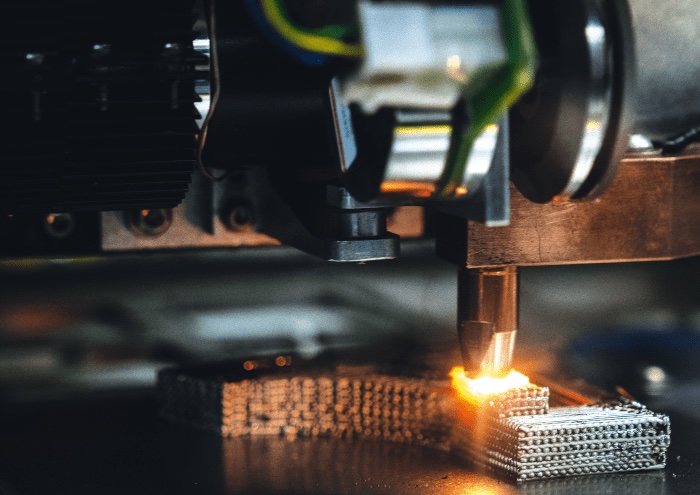
What you will find in this section
- Metal AM maturity index
- General Developments
- Laser Powder Bed Fusion
- Electron Beam Powder Bed Fusion
- Directed Energy Deposition
- Material Extrusion
- Binder Jetting
- Cold Spray
- Mold Slurry Deposition and Metal SLS
- Liquid Metal Printing
- Metal Lithography and Nano Particle Jetting
- Area-Wise VAT Polymerization
Industrialization and Technology Maturity Index
Evaluation with maturity index
To evaluate the different AM technologies AMPOWER has developed a model to characterize the maturity of an Additive Manufacturing technology based on two indices. The Industrialization Maturity Index and the Technology Maturity Index describe and compare the capabilities and adoption rate of each AM technology in the industrial environment. Both indices are crucial factors for evaluating the current status of any AM technology.
- The Technology Maturity Index evaluates the process capability, system reliability and availability as well as implemented quality control measures.
- The Industrialization Index assesses the supply chain, material availability, installed system base, public knowledge and research as well as standardization of each technology.
Each category is weighted according to its specific importance. Typically, the technological maturity increases first, and the industrialization follows. A detailed description of the current state of maturity is given in the deep dive section for each technology.

Technologies with AM Maturity Index “Prototype system” are still at an early development stage with in-house systems only or on the verge of first systems at beta-customers. Many of the technologies in this corridor are proprietary AM principles or just recently made public.
At a Maturity Index of “First application”, industrial adoption takes place and users introduce the technology in their R&D departments or machines are set up for pre serial production trials at beta-customers.
Technologies at a Maturity Index of “Industrial use” are on the verge of full industrialization. Technologies in this area have not yet been widely adopted as a serial manufacturing technology across multiple industries.
To reach “Widespread industrial use” the technology must be established in multiple industries as a production technology for functional end parts.
Due the industrial focus, AMPOWER does not rate technologies that are still in the proof-of-concept stage.
General Developments
A Maturing Market Faces Skepticism and Slower Innovation
The innovation speed of metal Additive Manufacturing technologies has noticeably decreased over the last few years. On the one hand, it shows a maturing market where single technologies such as Laser Beam Powder Bed Fusion or Wire DED have found applications where AM generates a significant benefit in product design, lead time, and ultimately cost. On the other hand, skepticism over the next “big thing” in AM technology has increased, questioning overhyped promises of new market entries and fading out technologies that failed to show industrial relevance over the last few years. These developments go hand in hand with a decreased speed in year-on-year maturity increase. Established AM technologies have reached a high technological maturity, reliably producing parts in the required quality in multiple industries, resulting in only incremental improvement in the Maturity Index. Increased pressure regarding industrial expectations and general competition between AM technologies hinders larger maturity leaps of less established technologies, as we have seen in the past.
Laser Powder Bed Fusion
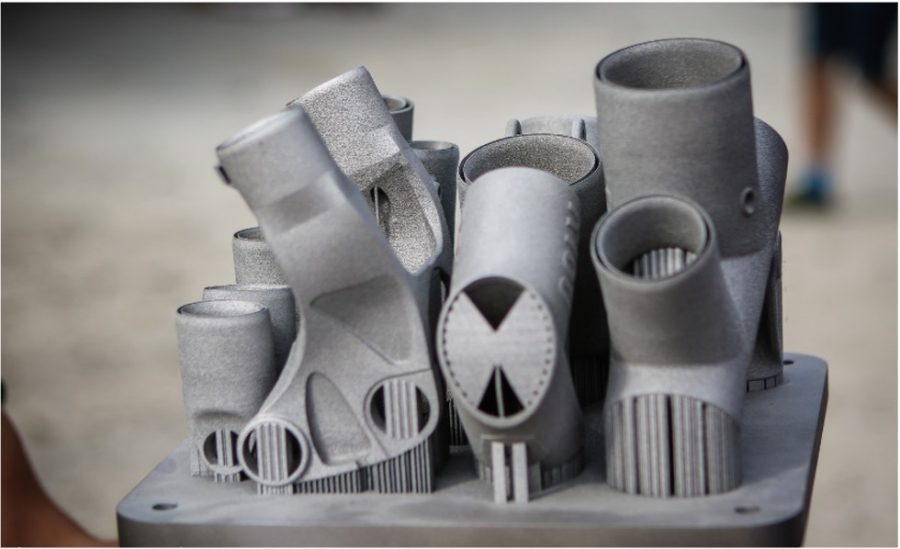
Technology Maturity Index: Very High
Industrialization Maturity Index: Very High
Laser Powder Bed Fusion holds on strong to its position as the premier metal AM technology. With the top spot in the Maturity Index, the latest developments of L-PBF have been more nuanced and targeted toward specific applications rather than large radical leaps. The technology is well established across multiple industries and applications, such as medical implants, turbine components, and tooling. Additionally, it finds increasing use in new applications for rocket engines, civil aviation, and even high-end sporting goods. In many of these industries, the long development and qualification cycles of AM will bear fruit when next-generation products containing multiple AM-designed components are launched in the near future.
The most prominent trend in L-PBF from 2023 continued in 2024 with the introduction of further very and ultra large machines. Following the pioneers of NIKON SLM SOLUTIONS and multiple Chinese OEMs, AMCM introduced its M8K system with a build envelope of 820x820x1,200 mm³ and eight 1 kW lasers. The system is specifically targeted at Defense and Space customers to print thrusters from Cu- and Ni-alloys. Currently, the largest machines on offer from Chinese OEMs BLT and EPLUS3D feature a build platform size of 1,550×1,500 mm² and 2,050×2,050 mm², respectively. Impressive in size, they are mostly installed in their domestic market. With an overall flatline sales volume based on units, the most successful OEMs were able to base their growth in 2024 on increased revenues from large and very large system sales.
Developments in the mid-size, multi-laser L-PBF systems continue to focus on machine individualization for specific applications rather than any specific technological advancements. For example, multiple suppliers introduced machines specifically targeting the Space industry with enlarged build chambers in the z-axis, higher laser power, or green lasers to manufacture rocket combustion chambers from copper alloys. Several PBF vendors now offer options for alternative laser spot caustics in a ring mode, providing potential benefits in processing for certain materials and applications.
The continuous climb in the Maturity Index of Area-wise Laser Powder Bed Fusion is slowing down for 2024. With only two companies in this category (SEURAT and VULCANFORMS) offering their own proprietary take on the technology, further market penetration is threatened by increased reservations towards a single-source supply chain. However, the slowdown in the Maturity Index does not necessarily hinder a future success story if technological innovation stays on track, delivering the promised cost per part. With large funding backing the development and first publicly announced development contracts for large volumes of metal parts, it is not unlikely that Area-wise L-PBF will continue to rise in the Maturity Index and reach “Industrial Use” within the next five years.
Electron Beam Powder Bed Fusion
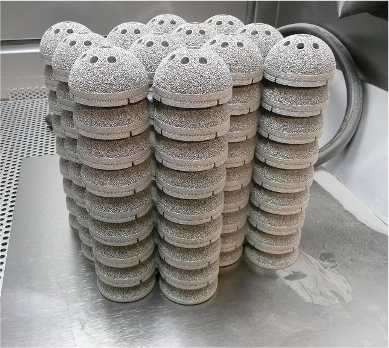
Technology Maturity Index: Very High
Industrialization Maturity Index: Very High
Electron Beam Powder Bed Fusion was able to rise in the Maturity Index, especially in its industrial maturity in 2024. The increased range of available machines since the market entry of MITSUBISHI ELECTRIC, JEOL, WAYLAND ADDITIVE, PRO-BEAM, and FREEMELT to formerly sole supplier COLIBRIUM ADDITIVE (formerly GE ADDITIVE, ARCAM) has led to wider acceptance and new areas of application for E-PBF. Additionally, to the established Ti- and TiAl-alloy applications in Medical and Aviation, the adoption rate in Oil and Gas, Space, and Industrial continuously increases. To distinguish itself from L-PBF, new E-PBF developments are often in high-temperature or refractory alloys targeting applications in rocket engines, nuclear reactors, or mining equipment.
Directed Energy Deposition
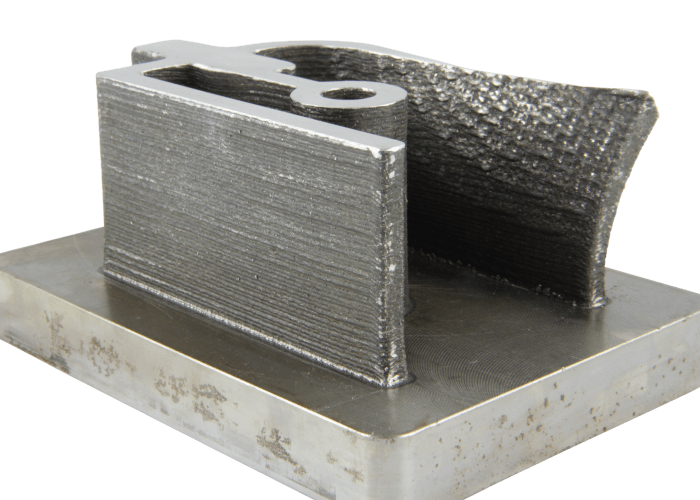
Technology Maturity Index: Very High
Industrialization Maturity Index: High
Powder Laser Energy Deposition has found its sweet spot in repair and coating applications. While debatable in which cases these applications are to be considered Additive Manufacturing, adding small features or complex repair operations is commonly marketed as AM. Although well established in rebuilding worn high-cost parts, e.g., turbine blade tips, the technology struggles to identify further non-coating business cases across multiple industries. The established supplier landscape and focused application field result in a high maturity index; however, with little to no movement over the last few years concerning AM.
Wire Laser Energy Deposition continuously rises in its technological and industrial maturity. Last year, multiple companies entered the market with interesting offers, and established players announced new developments. ACONITY3D and AMFREE released their first machines in 2024, serving different ends of the application spectrum. ACONITY3D, known for its highly individualizable and open L-PBF machines, entered the market with a small robot-based turnkey solution for a flexible AM production targeting a space currently dominated by MELTIO. On the other end, AMFREE released its AMFREE One system with up to 4 wires and 10 kW laser power for very high deposition rates, rivaling and outperforming Wire Arc competitors. Additionally, established players released new innovations. MELTIO introduced a new working head with 9 radially positioned blue direct diode lasers, aiming for higher efficiency and lower cost, while ADDERE delivered a Laser Wire ED system with 20 kW power and a build envelope of 5.6×2.5 m² to GKN AEROSPACE, pushing the limits of large-scale titanium AM components. Current developments indicate that Wire Laser Deposition will continue to successfully push into applications currently occupied by Wire Arc and Powder Laser ED.
After a big upward movement in the Maturity Index over the last years, Wire Electric and Plasma Arc Energy Deposition have established themselves as viable Additive Manufacturing production technologies for multiple applications and industries. The increasing production of titanium blanks for structural components with Plasma Arc ED in Aviation and lightweight parts for the High-Tech and Electronics industry is supporting the growth of established players such as WAAM3D and NORSK TITANIUM. While the first solely delivers parts printed on their proprietary in-house technology, the latter offers a wide range of machinery and ED technology for multiple applications. While plasma technology is focused on high-end components and materials, Wire Electric Arc is establishing itself in a wide range of applications. Currently, the largest application is the substitution of low-alloy castings, weighing up to 5,000 kg. AM can ease the increased pressure on the supply chain of low-volume castings regarding lead time and availability. LINCOLN ELECTRIC has established a production capacity of more than a dozen robot systems to serve this market. Additionally, applications in stainless steel and nickel-based alloys for the Energy, Oil and Gas, and Nuclear sectors are gathering further traction. Multiple companies such as AML3D, MX3D, and RAMLAB have installed multi-robot systems to enable parts of multiple meters in size. The demise of casting know-how and facilities in Western countries, undesired dependencies on forging capacities in “unfriendly” nations, and the increasing pressure for a sustainable manufacturing process will further support the switch to Wire Arc near-net-shape blank production in the next years.
Material Extrusion
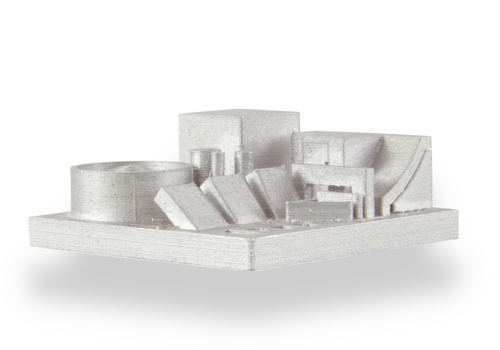
Technology Maturity Index: High
Industrialization Maturity Index: High
Although reaching the edge of “Industrial Use” in 2022, metal material extrusion technologies have failed to progress further in maturity since then. The persistent challenges along the complete process chain of Metal Filament Material Extrusion and Metal Pellet Material Extrusion, from the reliable prediction of shrinkage in the design phase to expertise in the sintering process, directly contradict the expectation of fast and efficient low-volume part production. The trial-and-error reality of the current production process makes these technologies an unlikely choice for widespread industrial use. Current developments in material extrusion technologies, including the metal slurry-based relative Dispersion Material Extrusion, are focusing on tooling applications, leveraging the ability to process alloy groups not available in L-PBF. A notable example is MANTLE3D, which utilizes a hybrid printing and milling process and focuses entirely on the production of tool inserts and conformal cooling tools. It is not expected that this technology group will advance into widespread industrial use but rather remain a solution for tooling and occasional spare part production.
Binder Jetting
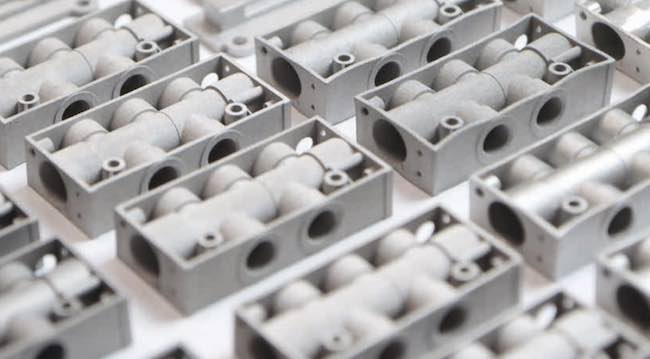
Technology Maturity Index: High
Industrialization Maturity Index: High
After turbulent past years, the hype around Binder Jetting has settled, and the technology has found multiple industrial applications. Most noticeably, Binder Jetting is used today in the luxury fashion, consumer electronics, medical instrument, and firearms industries. In all these industries, Binder Jetting is used to substitute small, complex milled parts or injection-molded parts in batch volumes smaller than 200,000 to 500,000. Higher flexibility and shorter development cycles compared to tool-bound sinter technologies are promoting an increased use of Binder Jetting, especially in consumer goods applications. In most cases, only experienced sintering suppliers like KENNAMETAL, GKN, and INDO-MIM can leverage the full potential of Binder Jetting due to their extensive knowledge and equipment along the complete process chain, from part design and distortion simulation to sintering expertise and furnace capacity to meet increasing demand.
Cold Spray
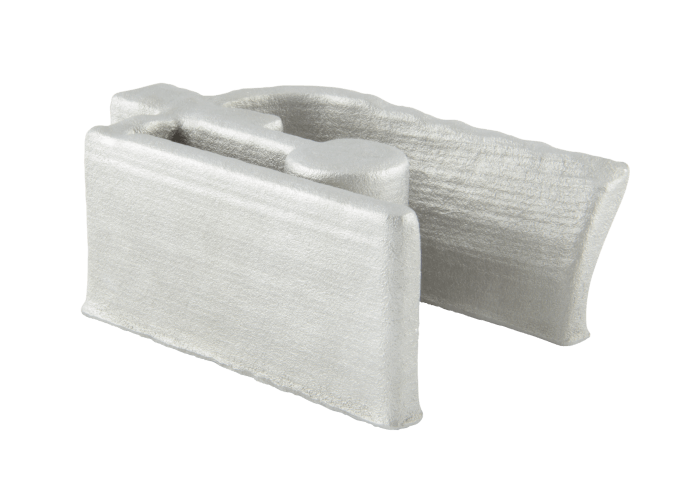
Technology Maturity Index: Medium
Industrialization Maturity Index: Medium
Cold Spray Additive Manufacturing did not advance in the Maturity Index in 2024. With predominantly two major players in this technology field (SPEE3D and TITOMIC) the current focus remains primarily on Defense and Space applications. Backed by current geopolitical developments, SPEE3D is promoting a compact, container-based solution for deployment in combat zones, enabling fast and easy repair and spare part production. TITOMIC targets applications involving titanium and steel, which they can process using their high-power gun and large stationary systems. With the current rise of Wire ED technologies, Cold Spray will need to prove its place in the AM landscape in the coming years to successfully reach “Industrial Use.”
Mold Slurry Deposition and Metal SLS
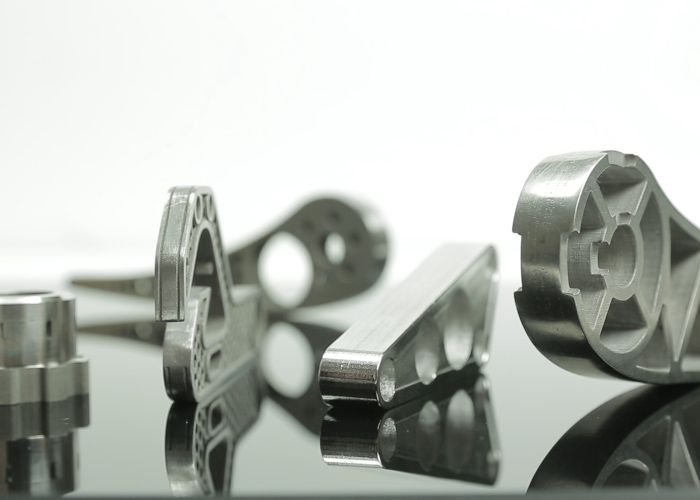
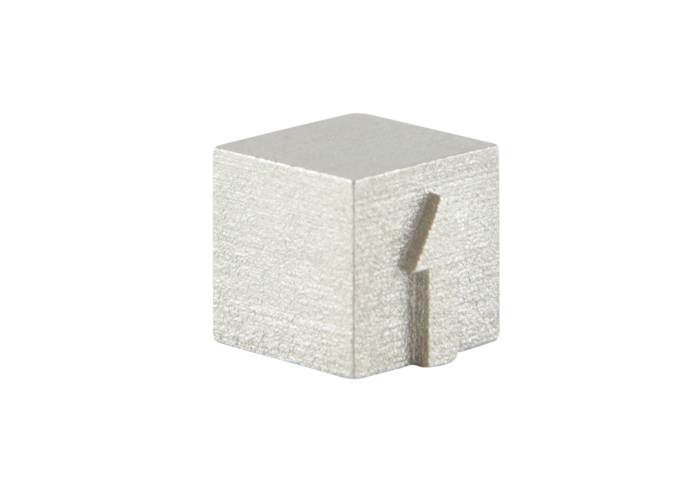
Technology Maturity Index: Medium
Industrialization Maturity Index: Medium
The increasing general awareness and knowledge of sinter AM technologies, pushed by the rise of Binder Jetting, have also benefited related technologies such as Mold Slurry Deposition and Metal SLS. Although proprietary, both technologies have found their first applications and customers and have advanced in industrial maturity towards “Industrial Use.” It will be interesting to see whether TRITONE and HEADMADE MATERIALS can overcome the typical skepticism of industrial users toward single-source technologies and achieve wider adoption in the coming years.
Liquid Metal Printing
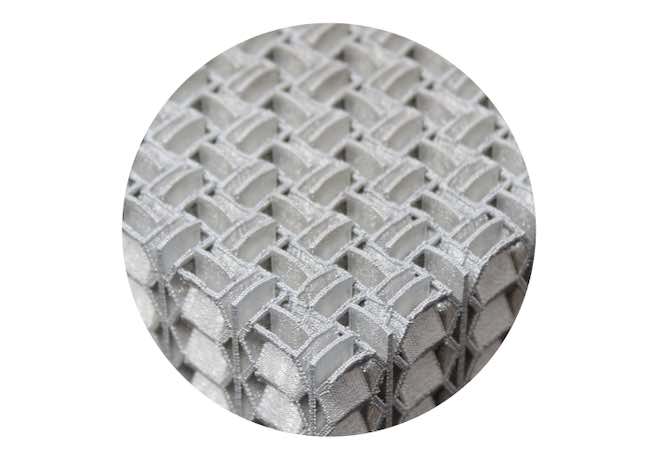
Technology Maturity Index: Medium
Industrialization Maturity Index: Medium
Liquid Metal Printing experienced a major setback in 2022 and therefore was not able to further advance in the Maturity Index. XEROX one of the leading technology providers discontinued its operation and halted all its R&D and sales activities. Fortunately, GROB-WERKE displayed its newly developed machine at Formnext 2022 to fill the gap XEROX is leaving. As an established CNC machine builder and manufacturing solutions provider in the automotive industry, GROB-WERKE aims to establish the technology for low volume castings and spare parts. The current and foreseeable limitations to low melting alloys will most likely prevent a wider spread industrial use in the foreseeable future.
Metal Lithography and Nano Particle Jetting
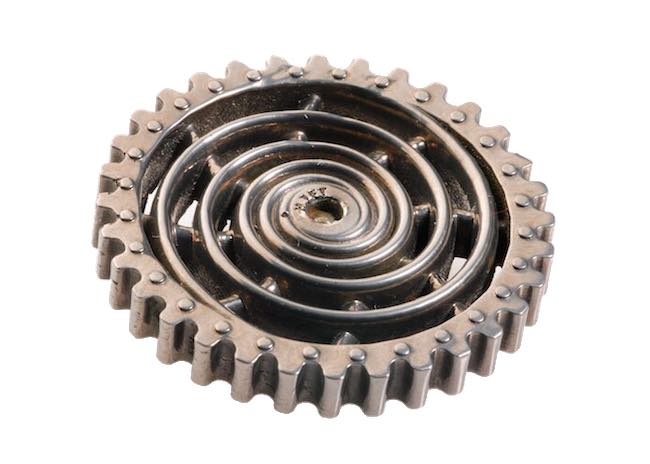
Technology Maturity Index: Medium
Industrialization Maturity Index: Medium
Metal Lithography and Nano Particle Jetting did not advance significantly over the last 12 months. Both technologies use a two-step process of 3D printing the green body and densifying the metal material in a final sintering step. While Metal Lithography creates the single layers in a liquid bed, Nano Particle Jetting creates the parts with direct droplet printing. Both technologies achieve very high resolutions and focus on small part applications. The strong focus on very small parts and lengthy technology development to create a robust process chain from start to finish have made it difficult to find many industrial applications. However, with a growing number of machine suppliers and the shipment of first machines to customers these technologies might find future applications in the medical, jewelry and electronics industry.
Friction Energy Deposition
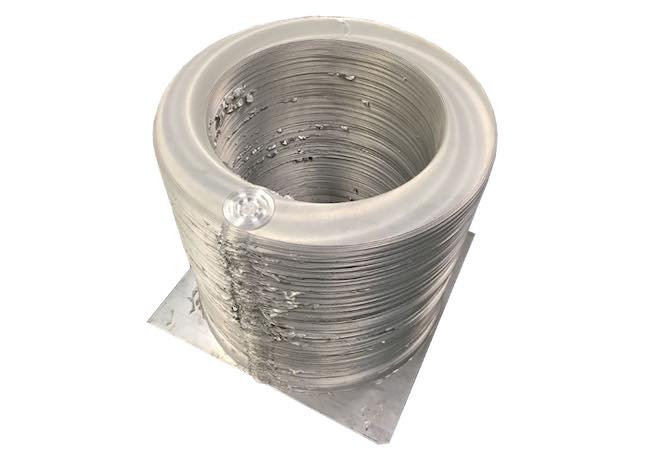
Technology Maturity Index: Medium
Industrialization Maturity Index: Medium
Friction Energy Deposition advanced in the Maturity Index in 2022. Since the technology is promoted by only a few machine suppliers it struggles to penetrate the AM and general technology market. Nonetheless, MELD was able to progress the technology and “win” first applications in the defense industry. Additionally, MELD launched its own part production service in 2023 to serve additional applications and industries with parts from its Friction Energy Deposition Technology.
Area-wise VAT Polymerization
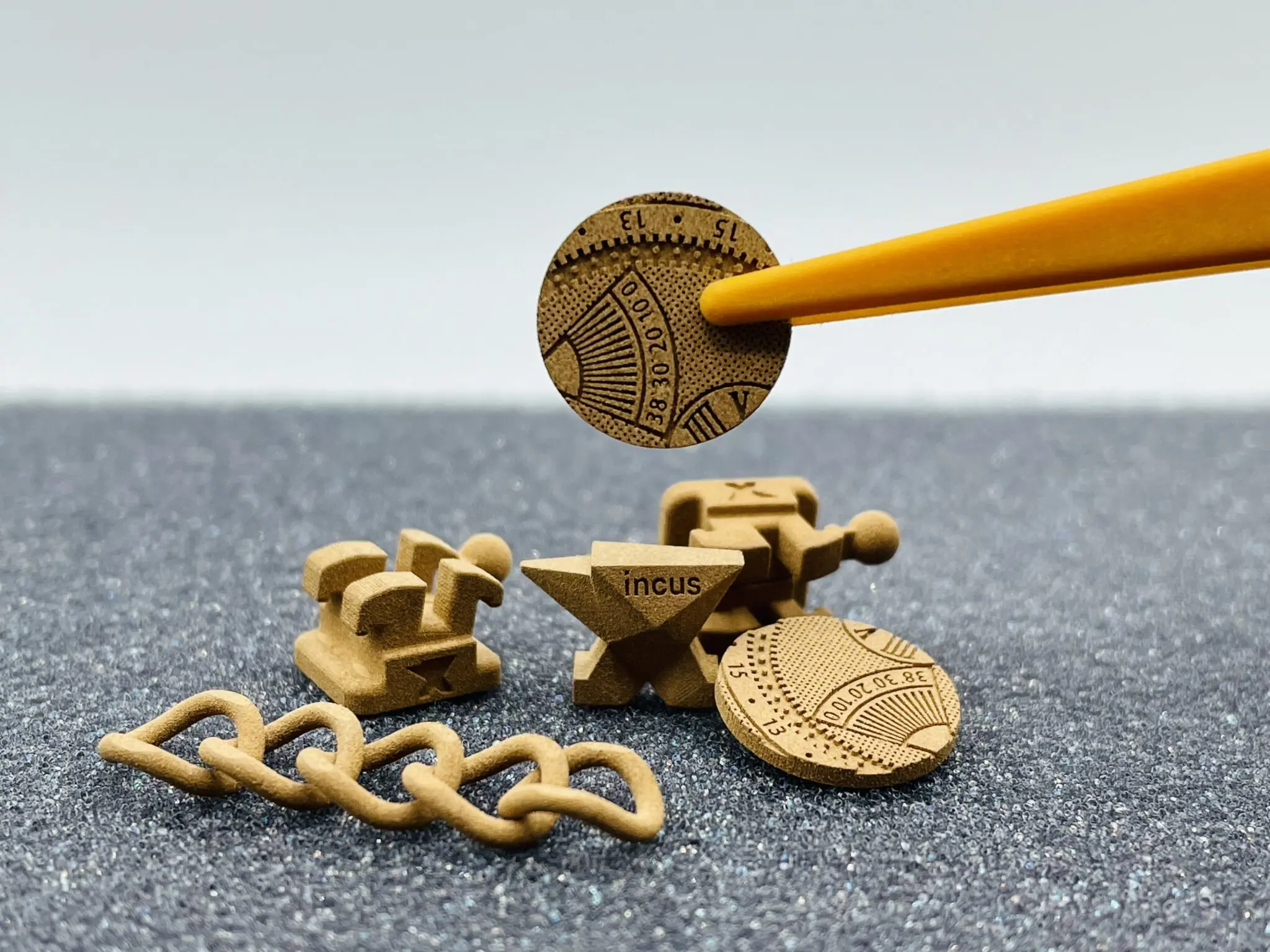
Technology Maturity Index: Medium
Industrialization Maturity Index: Medium
Two consecutive years of advancements in the Maturity Index place Area-Wise Vat Polymerization right in the middle of “First Applications.” New machine releases and further deliveries from INCUS to industrial customers justify these advancements. Customers use the technology to produce highly precise parts for the medical and jewelry industries. With the addition of 99.9% pure copper to the material portfolio, highly individualized and complex micro parts for the electronics industry are also potential future applications.