Cost comparison Connector
What are production costs for the connector?
This case study breaks down the production cost of a Connector for suitable technologies. Besides a breakdown of the total cost per part, the manufacturing time and cost per volume for different production quantities is provided.
What you will find in this section
Connector overview
Valve block not feasible for Material Extrusion and Binder Jetting
This case study breaks down the production cost of a Connector for Powder Bed Fusion (Laser and Electron Beam), Laser Metal Deposition (LMD) and Wire Arc Additive Manufacturing (WAAM). Due to too big dimensions of ⌀240 mm x 193 mm and volume of 1.956 cm³, the part is not feasible for Material Extrusion and Binder Jetting which are thus excluded from this comparison. The calculation is made for Stainless Steel 17-4PH, which is available for all technologies. The calculation is made for 10 parts, with a comparison of 1 part and 100 parts at the end.
The focus in this section lies exclusively on the cost estimation. The fact that the achievable part quality varies between the technologies must be kept in mind. Especially milling, which is not included in this comparison, will have a significant impact on the cost and lead time for the Connector.
The following post processing operations are included in the calculation:
- Unloading and unpacking of parts (All technologies)
- Heat Treatment (L-PBF, LMD, WAAM)
- Part separation (L-PBF, E-PBF)
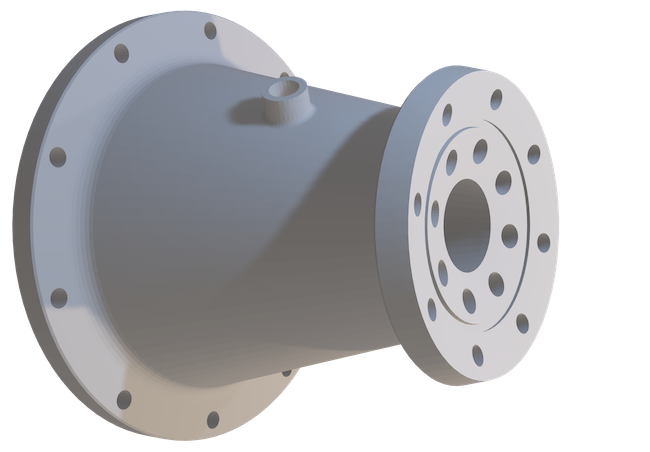
Cost per part (€ and %)
WAAM with lowest cost per part
The chart on the left compares the manufacturing cost per part for the 4 technologies.
WAAM is the cheapest process with total production costs of ~957 €. The low complexity and relatively big volume make this part an ideal candidate for the technology with low material costs and a high throughput.
Production costs for Laser Metal Deposition (LMD) are ~2.582 €. Costs are calculated using the low resolution nozzle, resulting in an effective build rate of ~67 cm³/h.
Laser Powder Bed Fusion (L-PBF) leads to cost per part of ~2.330 €. A medium-size system is chosen as the most cost-effective system since even most large systems would only fit 1 part. A high-productivity layer thickness of 90 µm leads to a high build rate of ~42 cm³/h.
Electron Beam Powder Bed Fusion (E-PBF) has the highest part costs of ~4.992 €. The relatively high cost are mainly driven by a lower layer thickness of 45 µm.
Production time
Wire Arc Additive Manufacturing with lower production time
The chart on the right compares the production time for 10 components between the different technologies. A WAAM printer is capable of producing all 10 components in less than 7 days, which is the main driver for the relatively low production costs. Even though the production time on a medium-sized L-PBF printer is higher compared to LMD, the lower hourly rate of the printer still leads to lower cost per part. E-PBF leads to the highest production time of close to 40 days due to the lower layer thickness.
Cost per cm³
No big price drop for higher quantities
When comparing the cost per cm³ for quantities ranging from 1 to 100 parts it can be observed that there is no big price drop with increased quantity for all technologies. This is mainly due to the fact that each technology produces 1 piece at a time and that build time per part is already relatively long.