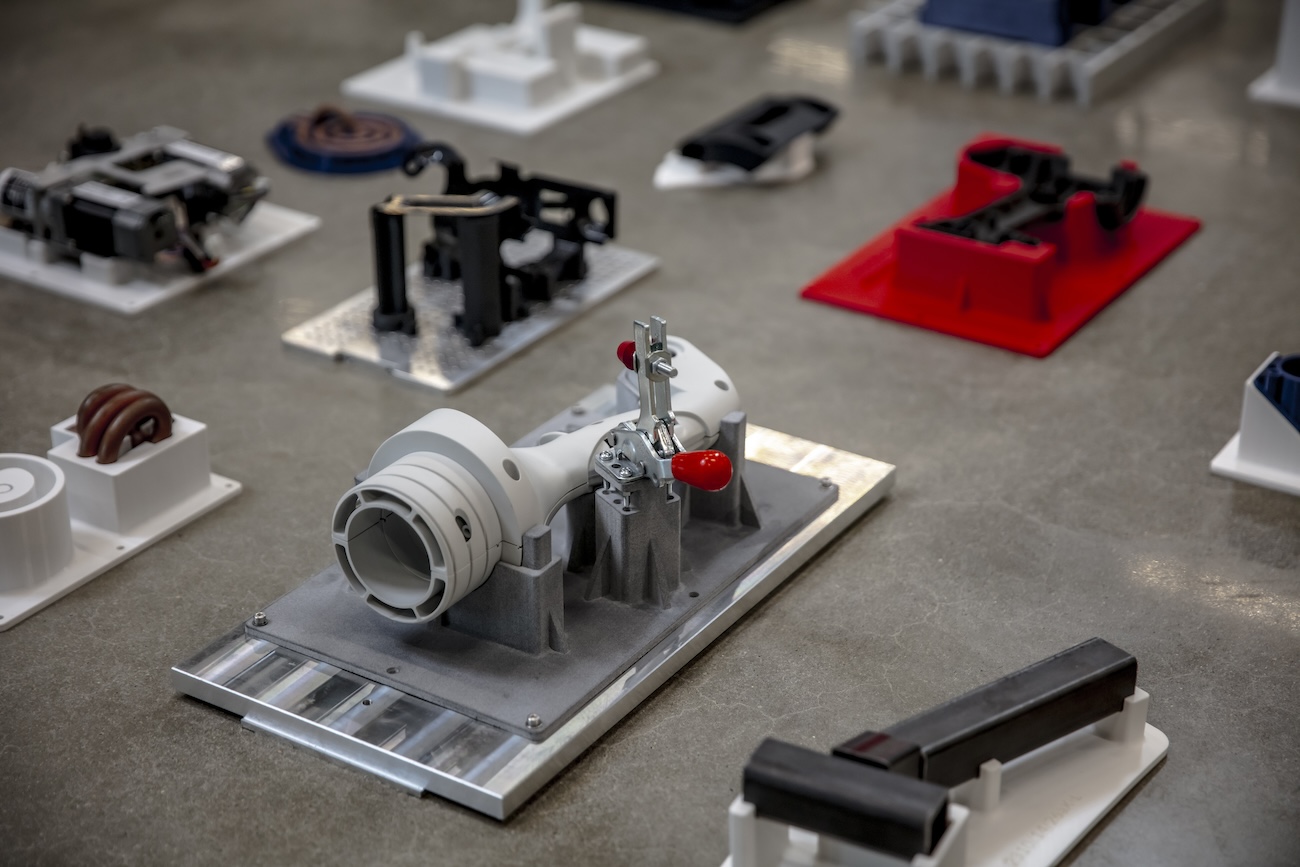
The power of 3D Printing and automated design for jigs & fixtures
AMPOWER Academy 3D Printing and automated design for jigs & fixtures Trinckle, Audi Sport, Deutsche Bahn Tooling, jigs & fixtures
Deutsche Bahn AG (DB AG) is the main German operator of transportation services and infrastructure. It offers mobility services, which include passenger rail and bus transportation, freight transportation, and railway infrastructure services. The company provides vehicle maintenance and security services. DB AG also offers conventional industrial energy products and develops and operates stations. The company also provides catering services, rail mobility management, communication technology products and operates global accounting shared service centres. It has operations in various countries across Europe, Asia-Pacific and North America. DB AG is headquartered in Berlin, Germany.
The 3D printing or Additive Manufacturing journey for Deutsche Bahn started in 2015. By 2023, the company has yet concluded 100.000 parts in 500 different applications using around 12 different AM technologies. The primary use cases are spare parts which can be found in various areas such as locomotives, wagons, infrastructure as well as train stations. 3D printing plays an important role at Deutsche Bahn as it enables much shorter and more cost-efficient repair cycles and increases the fleet and infrastructure availability. Trains are usually in operation for 30 years but in some cases even for over 50 years. After 15 years, spare parts can become more difficult to source and 3D Printing can successfully fill this gap. By digitalising the spare part inventory, the Deutsche Bahn now emerged as an early adopter and highly innovative company within the 3D printing industry. Besides spare parts, 3D printing is also strongly implemented at various DB sites for tools, jigs and fixtures. The technology saves time and money and sometimes even the operational performance is improved thus making the maintenance job on the shopfloor more efficient.
One of the most important learning for Deutsche Bahn is engagement. First, there is internal engagement with all relevant stakeholders. From engineering, quality management and maintenance staff to management. With specific applications that solve pressing problems, ensure vehicle availability, and may also save money, stakeholders can be convinced to further support the project or even get involved themselves. This starts with training and ends with internal, company wide marketing of success stories. While engineering and maintenance are triggered by applications that solve technical issues, management can be convinced by reduction of downtime during maintenance and cost savings, direct and throughout the lifecycle. Both areas are heavily addressed by the 3D printing applications which Deutsche Bahn has developed. The ideas for such applications often come from DB’s own employees who submit their printing suggestions, motivated by their own 3D Printing Competition.
But engagement also has an external component. Especially for companies, that cover multiple technologies and do not look at serial production of one single component, a vast network of partners can be vital for success. Especially exchanging with companies that have similar use cases can be extremely helpful. For Deutsche Bahn, those partners were found in other rail and mobility companies which led to the foundation of the Mobility goes Additive association. Topics that one single company can hardly cover such as materials, norms and standards are fast-tracked through this unique network in Europe.
Lesson 1
Get engaged - internally and externally
Many companies hire outside consultation to develop a 3D printing strategy long before their first actual parts are printed. At Deutsche Bahn, a “maker mentality” led to many initial use cases which tangibly helped to convince stakeholders and accelerate the adoption internally. Problem-solving use cases with a wow-effect in terms of size, quality, complexity and added value are more likely to convince both technology lovers as well as doubters. Even more important is that the initial use cases are not simply printed but carried through the whole process chain including testing and validation. Besides internal stakeholders, those proof-of-concept applications are last but not least important for external stakeholders as well as authorities.
Lesson 2
Proof the concepts and implement - impress lovers and doubters
The implementation journey of 3D printing as a clear change process for organisations is always a team challenge. If there is only one enthusiast, it is unlikely to become a success. A 3D printing team does not only consist of engineers but should also include team members on the maintenance shop floor on each site, quality managers, communication experts and procurement responsibles. Building this team is a key success factor. This means convincing and training of each team member, initiation of regular internal and external communication and the creation of a 3D printing team spirit with the ultimate goal to boost the efficiency of the company, reduce maintenance cost, and finally increase service quality and comfort for the end customer.
Learning 3
Shape a powerful team - you will love the ride!
3D printing has a very high potential in the spare parts industry. Deutsche Bahn has mastered to implement this technology through a long journey with the help of collaboration partners and by showing the full potential in over 500 specific use cases. This journey is still at its beginning. The ultimate aim is to create awareness for 3D printing possibilities within the whole company which will subsequently contribute to an increased vehicle availability and comfort for passengers plus higher internal efficiency of Deutsche Bahn.
AMPOWER Academy 3D Printing and automated design for jigs & fixtures Trinckle, Audi Sport, Deutsche Bahn Tooling, jigs & fixtures
AMPOWER Academy 3D printing at Eaton Aerospace Fueling progress: How Eaton Aerospace’s dedication to 3D Printing elevated aircraft performance Eaton
AMPOWER Academy 3D Printing in TRUMPF machines Collaborative Efforts, Expertise, and Know-How Lead to Thriving 3D Printing Applications in TRUMPF
Would you like to further advance your 3D Printing success story? We learned that training a broad number of employees is key to increase the usage of 3D Printing in a company and to successfully launch new applications.
You can try out the AM Fundamentals course of the AMPOWER Academy free of charge
Understand the most important topics to get started with Additive Manufacturing
The sinter-based AM (SBAM) technologies have, as the name suggests, the sintering process in common. In this process, the printed green part is consolidated into a dense part and receives its final properties. The green part can be printed in advance using different technologies.They all have in common that metal powder is bound to the desired shape by a binder. The best-known printing technologies include Binder Jetting and Filament Material Extrusion.
In this section, you learn everything about the sinter-based AM process chain and get an overview of the different printing technologies.
This course is aimed at engineers, designers and other professionals that are working closely with sinter-based AM technologies. The goal is to cover the most important aspects that will enable engineers and designers to fully grasp the capabilities and technical limitations of the printing technologies and the sintering process to succeed in technology selection and part design. Besides going through the course from the beginning until the end, this course can also act as a constant source of knowledge while working on AM projects.
The course is structured into the following sections.
This section will start with an overview of the sinter-based AM process chain and its printing technologies, followed by a technology deep dive into the most important aspects of the BJT technology, followed by a closer look at the debinding and sintering step also including sintering simulation .
The second section will provide an overview of the different materials that are available as well as part characteristics that can be achieved with the BJT process and typical methods for quality assurance. Finally, several common defects in the BJT process are presented.
The last section will act as a guideline for designers. Besides generally describing the process when designing for Additive Manufacturing, actionable restrictions and guidelines for the BJT process are provided. The final section will present several design examples from different industries.
Simulation to compensate the deformation during the sintering step, nesting of parts and definition of printing parameters
Through various printing processes, different feedstocks such as metal powders, filaments, pellets or dispersions are processed into green parts
Unpacking of fragile green parts needs to be done carefully and is typically a manual process.
Debinding describes the process of removing the binder which results in a brown part
To reach the structural integrity of a metal part, a sinter process is required. The powder particles fuse together to a coherent, solid structure via a mass transport that occurs at the atomic scale driven via diffusional forces.
The brown part shrinks ~13-21 % in each direction.
The process chain of sinter-based technologies differs from other AM Technologies. Especially the post-printing processes (debinding and sintering) are crucial to achieve the intended mechanical properties.
Binder Jetting is a powder based Additive Manufacturing technology in which a liquid polymer binder is selectively deposited onto the powder bed binding the metal particles and forming a green body.
The metal powder is applied to a build platform in a typical layer thickness of 40 µm to 100 µm. Subsequently a modified 2D print head apply a binder selectively onto the powder bed. Depending on machine technology a hardening or curing process of the binder is performed in parallel for each layer and/or at the end of the whole build. During the in-situ curing process a heat source is used to solidify the binder and form a solid polymer – metal powder composite.
Afterwards the build platform moves downward by the amount of one layer thickness and a new layer of powder is applied. Again, the liquid binder is deposited and hardened in the required regions of the next layer to form the green body. This process is repeated until the complete part is printed. After the complete printing process is finished the parts have to be removed from the “powder cake” meaning the surrounding loose but densified powder. To improve the removal of the excess powder from the green body often brushes or a blasting gun with air pressure are used.
To create a dense metal part the 3D printed green body has to be post-processed in a debinding and sintering process. Similar to the metal injection molding process BJT parts are placed in a high temperature furnace, where the binder is burnt out and the remaining metal particles are sintered together. The sintering results in densification of the 3D printed green body to a metal part with high densities of 97 % to 99,5%, dependent of the material.
In classic Binder Jetting systems such as the ones distributed by EXONE or DIGITAL METAL the liquid binding agent is selectively deposited with a single print head. Meaning the width of the print head does not cover the full width of the powder bed. Therefore, the print head moves multiple times in xy-direction over the powder bed to completely cover the printing area and distributing the polymer binder.
The SINGLE PASS JETTING technology was developed by DESKTOP METAL and HEWLETT PACKARD. The width of the printing head covers the full width of the powder bed. When the printhead passes over the powder bed, binder is released from more than 30,000 small nozzles and the whole powder layer is selectively immersed in binder in one pass. The process is bi-directional which means that the binder deposition takes place in both moving directions of the printhead. With these modifications the printing speed is significantly increased.
A similarly fast technology is the METAL JET process by HEWLETT PACKARD. In a single pass, a liquid printing agent is applied to the powder layer and subsequently partially evaporated to form the binding polymer around the metal powder. After the completion of the print an additional curing to achieve the full green body stability is needed.
3DEO combines the Binder Jetting process with a subsequent machining process. Different from conventional Binder Jetting processes, the binder is not only deposited selectively but onto the entire powder layer. After hardening of the complete layer, the part geometry is shaped through a milling process every couple of layers by cutting the part contour out of the binder powder composite.
Binder Jetting is a powder based Additive Manufacturing technology in which a liquid polymer binder is selectively deposited onto the powder bed binding the metal particles and forming a green body.
The metal powder is applied to a build platform in a typical layer thickness of 40 µm to 100 µm. Subsequently a modified 2D print head apply a binder selectively onto the powder bed. Depending on machine technology a hardening or curing process of the binder is performed in parallel for each layer and/or at the end of the whole build. During the in-situ curing process a heat source is used to solidify the binder and form a solid polymer – metal powder composite.
Binder Jetting is a powder based Additive Manufacturing technology in which a liquid polymer binder is selectively deposited onto the powder bed binding the metal particles and forming a green body.
The metal powder is applied to a build platform in a typical layer thickness of 40 µm to 100 µm. Subsequently a modified 2D print head apply a binder selectively onto the powder bed. Depending on machine technology a hardening or curing process of the binder is performed in parallel for each layer and/or at the end of the whole build. During the in-situ curing process a heat source is used to solidify the binder and form a solid polymer – metal powder composite.
Binder Jetting is a powder based Additive Manufacturing technology in which a liquid polymer binder is selectively deposited onto the powder bed binding the metal particles and forming a green body.
The metal powder is applied to a build platform in a typical layer thickness of 40 µm to 100 µm. Subsequently a modified 2D print head apply a binder selectively onto the powder bed. Depending on machine technology a hardening or curing process of the binder is performed in parallel for each layer and/or at the end of the whole build. During the in-situ curing process a heat source is used to solidify the binder and form a solid polymer – metal powder composite.
Binder Jetting is a powder based Additive Manufacturing technology in which a liquid polymer binder is selectively deposited onto the powder bed binding the metal particles and forming a green body.
The metal powder is applied to a build platform in a typical layer thickness of 40 µm to 100 µm. Subsequently a modified 2D print head apply a binder selectively onto the powder bed. Depending on machine technology a hardening or curing process of the binder is performed in parallel for each layer and/or at the end of the whole build. During the in-situ curing process a heat source is used to solidify the binder and form a solid polymer – metal powder composite.