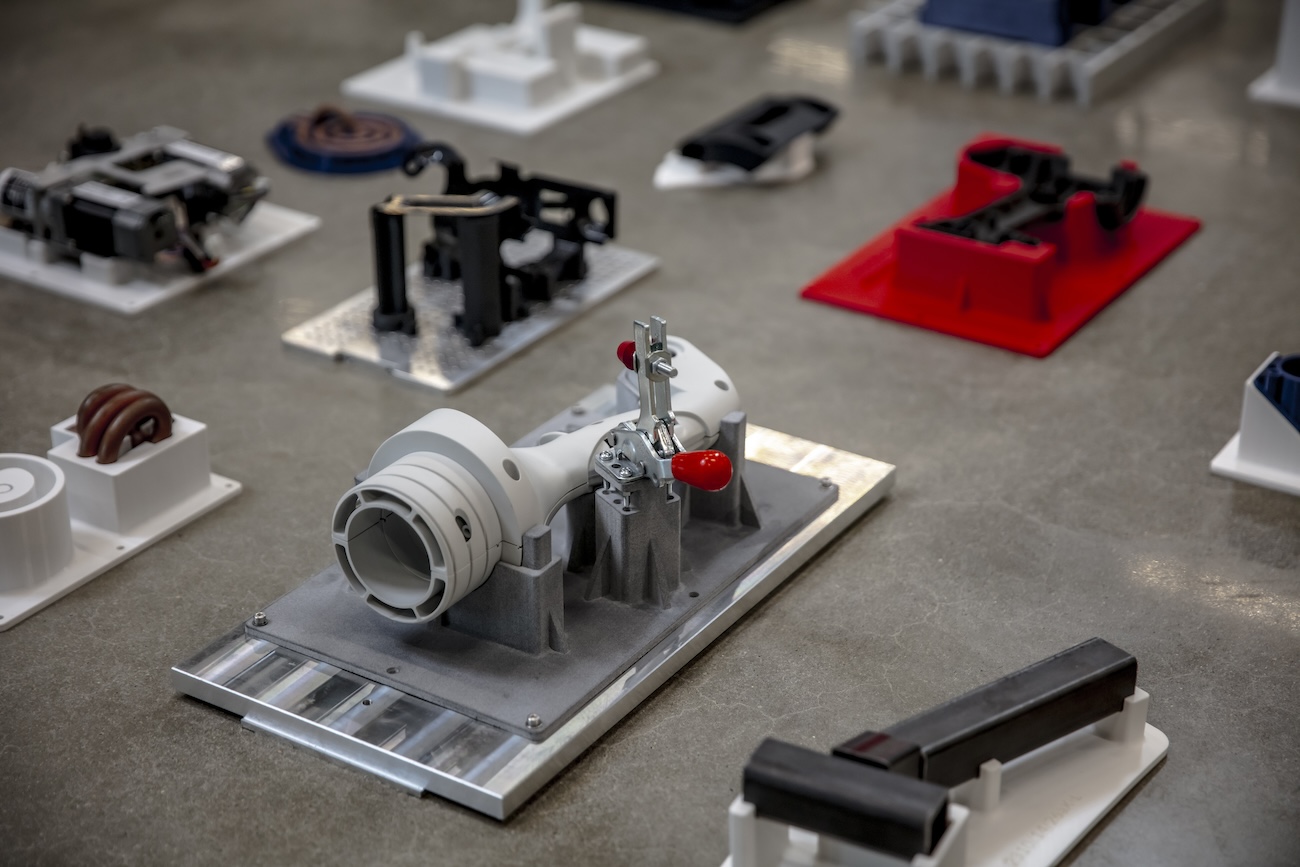
The power of 3D Printing and automated design for jigs & fixtures
AMPOWER Academy 3D Printing and automated design for jigs & fixtures Trinckle, Audi Sport, Deutsche Bahn Tooling, jigs & fixtures
EATON AEROSPACE is a leading aerospace company with a century-long history. The company designs, manufactures, and distributes advanced systems and components for aircrafts. Their wide range of products includes hydraulic, fuel, motion control, and electrical systems for commercial and military aircraft, helicopters, UAVs and space vehicles. With a global presence and collaborations with major manufacturers, they play a vital role in shaping the future of aerospace engineering, delivering innovative solutions for improved performance and efficiency.
Since 2016, EATON AEROSPACE has been developing 3D Printing and potential applications in the Aerospace sector. In 2020, 3 qualified components were strategically launched into serial production. 3 years later today, already 23 components have been awarded with EATON customers which is an impressive growth rate considering the high hurdles of Aerospace qualification efforts. As Michael York, Director of Additive Manufacturing at Eaton Aerospace, put it: “At Eaton Aerospace we are leveraging the power of Additive Manufacturing to produce superior products and systems”.
Reduced development time thus earlier go to market
Improved part performance such as optimized packaging, reduced weight, pressure drop (hydraulics) or improved heat management
Reduced cost
Increased sustainability
With this added value centric approach, the EATON AEROSPACE Management was deeply involved and committed regarding the implementation of 3D Printing and the necessary monetary and capacity investments. This strategy also involves a long-term commitment. It was clear from the beginning, that the success in 3D Printing does not come overnight but rather must be worked on for several years and the resulting applications today prove, that EATON AEROSPACE was very successful with this long-term approach.
Besides Management, the strategy also serves engineering as a guidance and motivation. Especially by solving today’s problems with 3D Printing and increasing performance of components is what increases awareness and support in engineering. Many companies in highly regulated industries such as Aviation or Medical still struggle because of a historically risk-averse engineering department. With this value-add centric 3D Printing strategy, EATON AEROSPACE was successfully involving all relevant stakeholders from senior management, product management, quality management and engineering.
Lesson 1
Success does not come overnight and without involving
everyone along the whole value chain. A long-term value
proposition focused vision and strategy helps the company to
stay on track.
Part of a 3D Printing strategy should be the focus on strategic projects. A company-wide training needs to be established, but it is just the beginning. Soon, pilot projects need to be identified that are being driven all the way through qualification so the company can prove the successful implementation in different business units before adapting the technology broader. Qualification procedures and quality management can learn along those pilot projects which accelerates later application implementations.
Lesson 2
Establish a selection of pilot projects that solve today’s
problems early on to focus qualification efforts. This will lead
to a hockey stick of applications later on.
EATON AEROSPACE has a relatively decentralized company structure, with engineering capacities in over 41 different facilities. This bears a challenge for every company that wants to implement a new manufacturing technology such as 3D Printing. EATON AEROSPACE tackled this challenge successfully by a dedicated structure for their 3D Printing approach. In addition to a deccentrally organization, a centralized “3D Printing Center of Excellence” was established in Charlson, South Carolina, where machine technology and additional intra-company services for design and printing of parts take place.
Learning 3
Establish a center of excellence and build up internal
knowledge before qualifying external suppliers.
EATON AEROSPACE has proven that 3D Printing is here to stay in Aerospace. The technology solves today’s manufacturing problems and improves part performance which reduces cost and increases sustainability on both ends, environment and supply chain. With those three learnings, EATON AEROSPACE was able to implement 3D Printing and set the basis for a high growth within the company in the coming years.
AMPOWER Academy 3D Printing and automated design for jigs & fixtures Trinckle, Audi Sport, Deutsche Bahn Tooling, jigs & fixtures
AMPOWER Academy 3D printing at Deutsche Bahn Deutsche Bahn Railway Berlin, Germany 26.09.2023 Share article Frankfurt (Main) Hbf – Einfahrt
AMPOWER Academy 3D Printing in TRUMPF machines Collaborative Efforts, Expertise, and Know-How Lead to Thriving 3D Printing Applications in TRUMPF
Would you like to further advance your 3D Printing success story? We learned that training a broad number of employees is key to increase the usage of 3D Printing in a company and to successfully launch new applications.
You can try out the AM Fundamentals course of the AMPOWER Academy free of charge
Understand the most important topics to get started with Additive Manufacturing
The sinter-based AM (SBAM) technologies have, as the name suggests, the sintering process in common. In this process, the printed green part is consolidated into a dense part and receives its final properties. The green part can be printed in advance using different technologies.They all have in common that metal powder is bound to the desired shape by a binder. The best-known printing technologies include Binder Jetting and Filament Material Extrusion.
In this section, you learn everything about the sinter-based AM process chain and get an overview of the different printing technologies.
This course is aimed at engineers, designers and other professionals that are working closely with sinter-based AM technologies. The goal is to cover the most important aspects that will enable engineers and designers to fully grasp the capabilities and technical limitations of the printing technologies and the sintering process to succeed in technology selection and part design. Besides going through the course from the beginning until the end, this course can also act as a constant source of knowledge while working on AM projects.
The course is structured into the following sections.
This section will start with an overview of the sinter-based AM process chain and its printing technologies, followed by a technology deep dive into the most important aspects of the BJT technology, followed by a closer look at the debinding and sintering step also including sintering simulation .
The second section will provide an overview of the different materials that are available as well as part characteristics that can be achieved with the BJT process and typical methods for quality assurance. Finally, several common defects in the BJT process are presented.
The last section will act as a guideline for designers. Besides generally describing the process when designing for Additive Manufacturing, actionable restrictions and guidelines for the BJT process are provided. The final section will present several design examples from different industries.
Simulation to compensate the deformation during the sintering step, nesting of parts and definition of printing parameters
Through various printing processes, different feedstocks such as metal powders, filaments, pellets or dispersions are processed into green parts
Unpacking of fragile green parts needs to be done carefully and is typically a manual process.
Debinding describes the process of removing the binder which results in a brown part
To reach the structural integrity of a metal part, a sinter process is required. The powder particles fuse together to a coherent, solid structure via a mass transport that occurs at the atomic scale driven via diffusional forces.
The brown part shrinks ~13-21 % in each direction.
The process chain of sinter-based technologies differs from other AM Technologies. Especially the post-printing processes (debinding and sintering) are crucial to achieve the intended mechanical properties.
Binder Jetting is a powder based Additive Manufacturing technology in which a liquid polymer binder is selectively deposited onto the powder bed binding the metal particles and forming a green body.
The metal powder is applied to a build platform in a typical layer thickness of 40 µm to 100 µm. Subsequently a modified 2D print head apply a binder selectively onto the powder bed. Depending on machine technology a hardening or curing process of the binder is performed in parallel for each layer and/or at the end of the whole build. During the in-situ curing process a heat source is used to solidify the binder and form a solid polymer – metal powder composite.
Afterwards the build platform moves downward by the amount of one layer thickness and a new layer of powder is applied. Again, the liquid binder is deposited and hardened in the required regions of the next layer to form the green body. This process is repeated until the complete part is printed. After the complete printing process is finished the parts have to be removed from the “powder cake” meaning the surrounding loose but densified powder. To improve the removal of the excess powder from the green body often brushes or a blasting gun with air pressure are used.
To create a dense metal part the 3D printed green body has to be post-processed in a debinding and sintering process. Similar to the metal injection molding process BJT parts are placed in a high temperature furnace, where the binder is burnt out and the remaining metal particles are sintered together. The sintering results in densification of the 3D printed green body to a metal part with high densities of 97 % to 99,5%, dependent of the material.
In classic Binder Jetting systems such as the ones distributed by EXONE or DIGITAL METAL the liquid binding agent is selectively deposited with a single print head. Meaning the width of the print head does not cover the full width of the powder bed. Therefore, the print head moves multiple times in xy-direction over the powder bed to completely cover the printing area and distributing the polymer binder.
The SINGLE PASS JETTING technology was developed by DESKTOP METAL and HEWLETT PACKARD. The width of the printing head covers the full width of the powder bed. When the printhead passes over the powder bed, binder is released from more than 30,000 small nozzles and the whole powder layer is selectively immersed in binder in one pass. The process is bi-directional which means that the binder deposition takes place in both moving directions of the printhead. With these modifications the printing speed is significantly increased.
A similarly fast technology is the METAL JET process by HEWLETT PACKARD. In a single pass, a liquid printing agent is applied to the powder layer and subsequently partially evaporated to form the binding polymer around the metal powder. After the completion of the print an additional curing to achieve the full green body stability is needed.
3DEO combines the Binder Jetting process with a subsequent machining process. Different from conventional Binder Jetting processes, the binder is not only deposited selectively but onto the entire powder layer. After hardening of the complete layer, the part geometry is shaped through a milling process every couple of layers by cutting the part contour out of the binder powder composite.
Binder Jetting is a powder based Additive Manufacturing technology in which a liquid polymer binder is selectively deposited onto the powder bed binding the metal particles and forming a green body.
The metal powder is applied to a build platform in a typical layer thickness of 40 µm to 100 µm. Subsequently a modified 2D print head apply a binder selectively onto the powder bed. Depending on machine technology a hardening or curing process of the binder is performed in parallel for each layer and/or at the end of the whole build. During the in-situ curing process a heat source is used to solidify the binder and form a solid polymer – metal powder composite.
Binder Jetting is a powder based Additive Manufacturing technology in which a liquid polymer binder is selectively deposited onto the powder bed binding the metal particles and forming a green body.
The metal powder is applied to a build platform in a typical layer thickness of 40 µm to 100 µm. Subsequently a modified 2D print head apply a binder selectively onto the powder bed. Depending on machine technology a hardening or curing process of the binder is performed in parallel for each layer and/or at the end of the whole build. During the in-situ curing process a heat source is used to solidify the binder and form a solid polymer – metal powder composite.
Binder Jetting is a powder based Additive Manufacturing technology in which a liquid polymer binder is selectively deposited onto the powder bed binding the metal particles and forming a green body.
The metal powder is applied to a build platform in a typical layer thickness of 40 µm to 100 µm. Subsequently a modified 2D print head apply a binder selectively onto the powder bed. Depending on machine technology a hardening or curing process of the binder is performed in parallel for each layer and/or at the end of the whole build. During the in-situ curing process a heat source is used to solidify the binder and form a solid polymer – metal powder composite.
Binder Jetting is a powder based Additive Manufacturing technology in which a liquid polymer binder is selectively deposited onto the powder bed binding the metal particles and forming a green body.
The metal powder is applied to a build platform in a typical layer thickness of 40 µm to 100 µm. Subsequently a modified 2D print head apply a binder selectively onto the powder bed. Depending on machine technology a hardening or curing process of the binder is performed in parallel for each layer and/or at the end of the whole build. During the in-situ curing process a heat source is used to solidify the binder and form a solid polymer – metal powder composite.