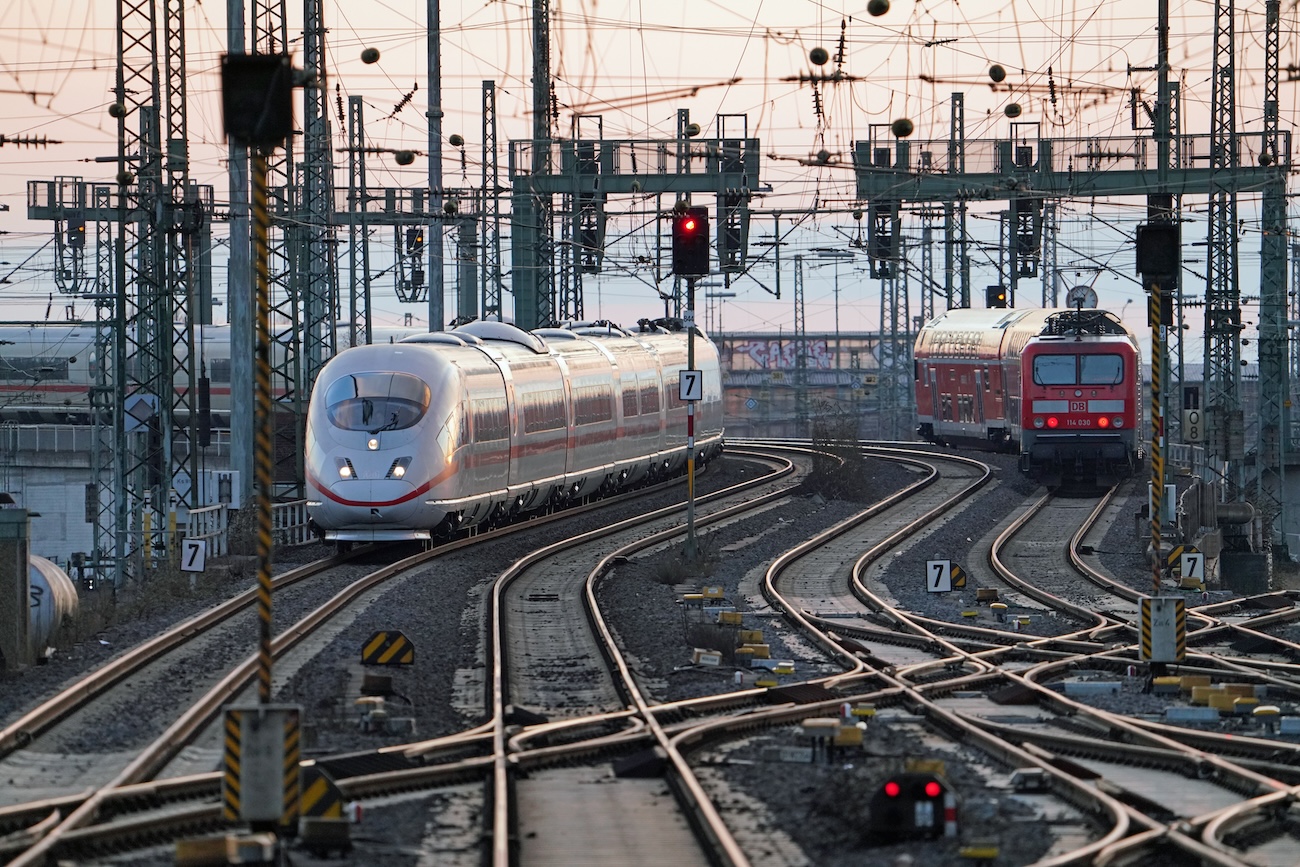
3D printing at Deutsche Bahn
AMPOWER Academy 3D printing at Deutsche Bahn Deutsche Bahn Railway Berlin, Germany 26.09.2023 Share article Frankfurt (Main) Hbf – Einfahrt
In the area of industrial tooling, the demand for customized solutions has never been greater. Conventional manufacturing technologies often struggle to keep pace with increasing production needs, leading to inefficiencies and generic solutions. However, with the development of 3D printing technologies, companies are reshaping the landscape of tooling, jigs and fixtures.
Jigs, fixtures, and other manufacturing aids are a great fit for 3D printing, but companies often struggle when it comes to creating the designs. Designing parts manually consumes considerable time and resources from engineers, leading to increased costs and extended delivery times. A growing number of companies such as Audi Sport and Deutsche Bahn have discovered an optimized solution: Automated design software by companies such as trinckle.
fixturemate, their specialized software, empowers users to effortlessly design and customize tools, jigs, and fixtures, leading to significant reductions in part costs and delivery times. It also allows more people to participate in the design process, keeping designs closely aligned with the users’ needs and freeing up skilled engineers for higher priority tasks.
The limitations of manual design processes is something the tooling industry has struggled with for a long time. Historically, creating tools, jigs and fixtures has been a specialized, time-consuming process which results in generic solutions that fail to adapt to the diverse needs of automated industrial operations. With the rise of automation and constantly changing production processes, the demand for individualized solutions has dramatically increased, presenting a significant challenge to manufacturers.
3D printing technologies provide a solution to these challenges by enabling customized components to be manufactured in batch sizes as small as one, revolutionizing the conventional one-size-fits-all approach. This means lightweight, robust tools tailored to specific applications and processes can be manufactured, leading to better efficiency and flexibility in industrial environments. Most metal and polymer 3D printing technologies can be used to create tools, jigs and fixtures, but low-cost technologies such extrusion-based 3D printing are a great fit: They lead to low cost-per-part and a quick return on investment. They are also easy to use and a good use case for the technology beyond prototyping.
Besides the manufacturing of parts, creating designs is a major challenge for companies. Manually designing parts with CAD software requires significant time and specialized engineering resources, which can lead to higher design costs and longer delivery times. To address this, companies across various industries, including automotive and transport, have turned to automated design tools. One such solution is fixturemate by trinckle, which streamlines the design process and reduces complexity.
The following case studies show insights into how various companies have used fixturemate to streamline design workflows to produce 3D printed tools, jigs, and fixtures.
Audi Sport is the high-performance car manufacturing subsidiary of Audi, responsible for vehicles such as the Audi RS3, the Audi R8, as well as performance racing cars. Compared to mainstream car manufacturers, the variety of vehicles is high, requiring a broad range of specialized tools, jigs, and fixtures during their production. For example, during the production of Audi e-tron GT, Audi Sport needed to design approximately 200 new fixtures, jigs, and other tools. Traditionally, each of these items requires a skilled engineer to manually design it in CAD software, diverting important resources from the more challenging aspects of automotive production.
To solve these challenges, Audi Sport has used fixturemate from trinckle. This design automation software can be used by engerinners as well as trainees. The software also gives additional flexibility for last-minute changes, making the design process more accessible and keeping design accuracy high. Using the software, operational efficiency is enhanced: The average design time can be reduced from approximately 2 – 4 hours to 10 – 20 minutes per design, which marks a 95% time saving. 3D printing the parts leads to a cost reduction of 80% and cuts delivery time from 6 weeks to 48 hours.
"In CAD we usually need two to four hours to produce a design, depending on the size of the part. With fixturemate we can produce a usable fixture in minutes. Because it's easy to use, we can bring in trainees and show them how to use it."
Cem Guelaylar, Additive Manufacturing Lead, Audi Sport GmbH
Deutsche Bahn is the main German operator of transportation services and infrastructure and has over 300,000 employees. The company operates a high number of trains and other infrastructure from different generations, making maintenance a challenging task. Deutsche Bahn’s engineering team is therefore focusing on improving maintenance efficiency across their many facilities. Despite many design ideas for fixtures, limited access to design personnel and CAD tools creates a design bottleneck which hinders the maintenance of customized parts.
fixturemate provides Deutsche Bahn with a solution forby democratizing the design work to a wider range of employees. Besides speeding up the design process, the software allows for the standardization of key components such as baseplates. The simplicity of the software fosters innovation and improves 3D printing processes, eliminating the need for costly CAD tools and specialized skills.
"Trinckle's Fixturemate software has seamlessly integrated design automation into our additive manufacturing processes for tooling at Deutsche Bahn, particularly for 3D printing assembly fixtures and carrier systems. The software has drastically reduced our design times and costs. Even without special hardware or expertise, the software can be easily used in a web browser by anyone at DB, driving the adoption of additive manufacturing."
Sven Gaede, Application Engineer Additive Manufacturing
trinckle develops software solutions for the age of additive manufacturing, commonly known as 3D printing. Their flagship product, fixturemate, empowers any user to design custom fixtures in under 20 minutes without needing CAD expertise. All trinckle applications are powered by their paramate engine, enabling robust custom design automation solutions that streamline workflows and provide an intuitive platform for smart product configuration.
AMPOWER Academy 3D printing at Deutsche Bahn Deutsche Bahn Railway Berlin, Germany 26.09.2023 Share article Frankfurt (Main) Hbf – Einfahrt
AMPOWER Academy 3D printing at Eaton Aerospace Fueling progress: How Eaton Aerospace’s dedication to 3D Printing elevated aircraft performance Eaton
AMPOWER Academy 3D Printing in TRUMPF machines Collaborative Efforts, Expertise, and Know-How Lead to Thriving 3D Printing Applications in TRUMPF
Would you like to further advance your 3D Printing success story? We learned that training a broad number of employees is key to increase the usage of 3D Printing in a company and to successfully launch new applications.
You can try out the AM Fundamentals course of the AMPOWER Academy free of charge
Understand the most important topics to get started with Additive Manufacturing
The sinter-based AM (SBAM) technologies have, as the name suggests, the sintering process in common. In this process, the printed green part is consolidated into a dense part and receives its final properties. The green part can be printed in advance using different technologies.They all have in common that metal powder is bound to the desired shape by a binder. The best-known printing technologies include Binder Jetting and Filament Material Extrusion.
In this section, you learn everything about the sinter-based AM process chain and get an overview of the different printing technologies.
This course is aimed at engineers, designers and other professionals that are working closely with sinter-based AM technologies. The goal is to cover the most important aspects that will enable engineers and designers to fully grasp the capabilities and technical limitations of the printing technologies and the sintering process to succeed in technology selection and part design. Besides going through the course from the beginning until the end, this course can also act as a constant source of knowledge while working on AM projects.
The course is structured into the following sections.
This section will start with an overview of the sinter-based AM process chain and its printing technologies, followed by a technology deep dive into the most important aspects of the BJT technology, followed by a closer look at the debinding and sintering step also including sintering simulation .
The second section will provide an overview of the different materials that are available as well as part characteristics that can be achieved with the BJT process and typical methods for quality assurance. Finally, several common defects in the BJT process are presented.
The last section will act as a guideline for designers. Besides generally describing the process when designing for Additive Manufacturing, actionable restrictions and guidelines for the BJT process are provided. The final section will present several design examples from different industries.
Simulation to compensate the deformation during the sintering step, nesting of parts and definition of printing parameters
Through various printing processes, different feedstocks such as metal powders, filaments, pellets or dispersions are processed into green parts
Unpacking of fragile green parts needs to be done carefully and is typically a manual process.
Debinding describes the process of removing the binder which results in a brown part
To reach the structural integrity of a metal part, a sinter process is required. The powder particles fuse together to a coherent, solid structure via a mass transport that occurs at the atomic scale driven via diffusional forces.
The brown part shrinks ~13-21 % in each direction.
The process chain of sinter-based technologies differs from other AM Technologies. Especially the post-printing processes (debinding and sintering) are crucial to achieve the intended mechanical properties.
Binder Jetting is a powder based Additive Manufacturing technology in which a liquid polymer binder is selectively deposited onto the powder bed binding the metal particles and forming a green body.
The metal powder is applied to a build platform in a typical layer thickness of 40 µm to 100 µm. Subsequently a modified 2D print head apply a binder selectively onto the powder bed. Depending on machine technology a hardening or curing process of the binder is performed in parallel for each layer and/or at the end of the whole build. During the in-situ curing process a heat source is used to solidify the binder and form a solid polymer – metal powder composite.
Afterwards the build platform moves downward by the amount of one layer thickness and a new layer of powder is applied. Again, the liquid binder is deposited and hardened in the required regions of the next layer to form the green body. This process is repeated until the complete part is printed. After the complete printing process is finished the parts have to be removed from the “powder cake” meaning the surrounding loose but densified powder. To improve the removal of the excess powder from the green body often brushes or a blasting gun with air pressure are used.
To create a dense metal part the 3D printed green body has to be post-processed in a debinding and sintering process. Similar to the metal injection molding process BJT parts are placed in a high temperature furnace, where the binder is burnt out and the remaining metal particles are sintered together. The sintering results in densification of the 3D printed green body to a metal part with high densities of 97 % to 99,5%, dependent of the material.
In classic Binder Jetting systems such as the ones distributed by EXONE or DIGITAL METAL the liquid binding agent is selectively deposited with a single print head. Meaning the width of the print head does not cover the full width of the powder bed. Therefore, the print head moves multiple times in xy-direction over the powder bed to completely cover the printing area and distributing the polymer binder.
The SINGLE PASS JETTING technology was developed by DESKTOP METAL and HEWLETT PACKARD. The width of the printing head covers the full width of the powder bed. When the printhead passes over the powder bed, binder is released from more than 30,000 small nozzles and the whole powder layer is selectively immersed in binder in one pass. The process is bi-directional which means that the binder deposition takes place in both moving directions of the printhead. With these modifications the printing speed is significantly increased.
A similarly fast technology is the METAL JET process by HEWLETT PACKARD. In a single pass, a liquid printing agent is applied to the powder layer and subsequently partially evaporated to form the binding polymer around the metal powder. After the completion of the print an additional curing to achieve the full green body stability is needed.
3DEO combines the Binder Jetting process with a subsequent machining process. Different from conventional Binder Jetting processes, the binder is not only deposited selectively but onto the entire powder layer. After hardening of the complete layer, the part geometry is shaped through a milling process every couple of layers by cutting the part contour out of the binder powder composite.
Binder Jetting is a powder based Additive Manufacturing technology in which a liquid polymer binder is selectively deposited onto the powder bed binding the metal particles and forming a green body.
The metal powder is applied to a build platform in a typical layer thickness of 40 µm to 100 µm. Subsequently a modified 2D print head apply a binder selectively onto the powder bed. Depending on machine technology a hardening or curing process of the binder is performed in parallel for each layer and/or at the end of the whole build. During the in-situ curing process a heat source is used to solidify the binder and form a solid polymer – metal powder composite.
Binder Jetting is a powder based Additive Manufacturing technology in which a liquid polymer binder is selectively deposited onto the powder bed binding the metal particles and forming a green body.
The metal powder is applied to a build platform in a typical layer thickness of 40 µm to 100 µm. Subsequently a modified 2D print head apply a binder selectively onto the powder bed. Depending on machine technology a hardening or curing process of the binder is performed in parallel for each layer and/or at the end of the whole build. During the in-situ curing process a heat source is used to solidify the binder and form a solid polymer – metal powder composite.
Binder Jetting is a powder based Additive Manufacturing technology in which a liquid polymer binder is selectively deposited onto the powder bed binding the metal particles and forming a green body.
The metal powder is applied to a build platform in a typical layer thickness of 40 µm to 100 µm. Subsequently a modified 2D print head apply a binder selectively onto the powder bed. Depending on machine technology a hardening or curing process of the binder is performed in parallel for each layer and/or at the end of the whole build. During the in-situ curing process a heat source is used to solidify the binder and form a solid polymer – metal powder composite.
Binder Jetting is a powder based Additive Manufacturing technology in which a liquid polymer binder is selectively deposited onto the powder bed binding the metal particles and forming a green body.
The metal powder is applied to a build platform in a typical layer thickness of 40 µm to 100 µm. Subsequently a modified 2D print head apply a binder selectively onto the powder bed. Depending on machine technology a hardening or curing process of the binder is performed in parallel for each layer and/or at the end of the whole build. During the in-situ curing process a heat source is used to solidify the binder and form a solid polymer – metal powder composite.